Gold leaching pretreatment is a process that is used to improve the overall efficiency of the leaching process. The pretreatment goal is to remove any impurities from the gold ore and reduce the size of the gold particles. The pretreatments make gold easier to leach and extract gold from the ore more complete. There are different gold leachings pretreatment methods, such as roasting and bacterial oxidation pretreatment. Each of them has its benefits and drawbacks. Follow me to recognize them.
Roasting Oxidation Pretreatment
The roasting oxidation method is traditional in non-ferrous metal beneficiation and smelting. It is also the most common and reliable method for treating gold-bearing sulfide ores, especially carbon-bearing sulfide ores.
The purpose of roasting
- Decompose the sulfide to expose the gold grains.
- Volatilize the sulfides of arsenic and antimony in an oxidized state, and charcoal burns or loses activity.
- Relatively enrich microscopic or submicroscopic fine-grained gold to provide good kinetic conditions for the next step of cyanide leaching gold.
Influencing factors
Roasting is a multiphase chemical reaction process, and its main influencing factors are:
- Physicochemical properties of reactants and products (particle size, porosity, chemical composition, etc.).
- Airflow characteristics.
- Oxygen concentration in the gas phase.
The selection of temperature and the control of conditions is essential, so the roasting method is very sensitive to operating parameters and feed ingredients, which often results in over-burning or under-burning so that the leaching rate of calcining is not high.
Advantages and disadvantages
The traditional roasting process will release many toxic gases such as SO2 and As2O3 during the roasting process, which will seriously pollute the environment; the dust collection and purification device of the furnace gas is complicated, and the operation cost is high. However, the roasting method is simple and reliable, and the advantages of comprehensive recovery of S, As, and other elements make it endlessly enjoyable.
To solve the defects of under-burning, over-burning, and environmental pollution, scientific and technological workers have continued to research and explore over the years so that the roasting process and equipment have been continuously improved and developed. As far as equipment is concerned, it has developed from a single hearth furnace to a multiple hearth furnace and from a fixed bed to fluidized boiling roasting. In terms of technology, it is developed from one stage to two or more stages of roasting, from air to oxygen-enriched roasting. In addition, based on the traditional process, adding salt to fix sulfur and arsenic roasting has been developed, which solves the problem of environmental pollution caused by the escape of sulfur and arsenic oxides. It reduces the burden of exhaust gas purification and dust removal. Oxidative and sulfated roasting, reduction roasting, oxidative roasting, and salt-added roasting are some new roasting processes developed based on traditional roasting methods in recent years. These methods have their characteristics in addition to some characteristics of the traditional roasting process.
Oxidation and sulfation roasting are widely used to treat Fe, Cu, Cu-Ni, Co, Mn, Zn, Sb, and other sulfide ores. It converts heavy metals into soluble metal oxides or sulfates, turns iron into insoluble iron oxide, and makes carbonaceous substances burn As, Sb, Se, and Pb to volatilize as gaseous oxides. The extraction rate of gold after roasting is greatly improved.
Salt-added roasting is a technology developed in response to the problems of high environmental pollution and heavy exhaust gas purification burden in the traditional roasting process of gold mines with high S and As content. For As, the commonly used salts are Na2CO3/NaHCO3 and calcium salts (CaCl2, Ca(OH)2).
Oxidative roasting is a mature industrial method, and the effect of removing As is good. But it will cause serious environmental pollution because the roasting process generates As2O3 and SO2 (it is difficult to produce sulfuric acid if it contains As2O3). And it can’t completely remove As because roasting generates non-volatile arsenate and arsenide. Au is passivated by fusible Fe and As compounds. It can’t achieve a high recovery rate when cyaniding calcine contains Fe. It requires alkaline or acid leaching to dissolve the passivation film, then re-grinding and floating. Although the oxidative roasting method can improve the recovery rate of Au, it is not easy to realize in the industry. It can see that other methods will replace oxidative roasting soon.
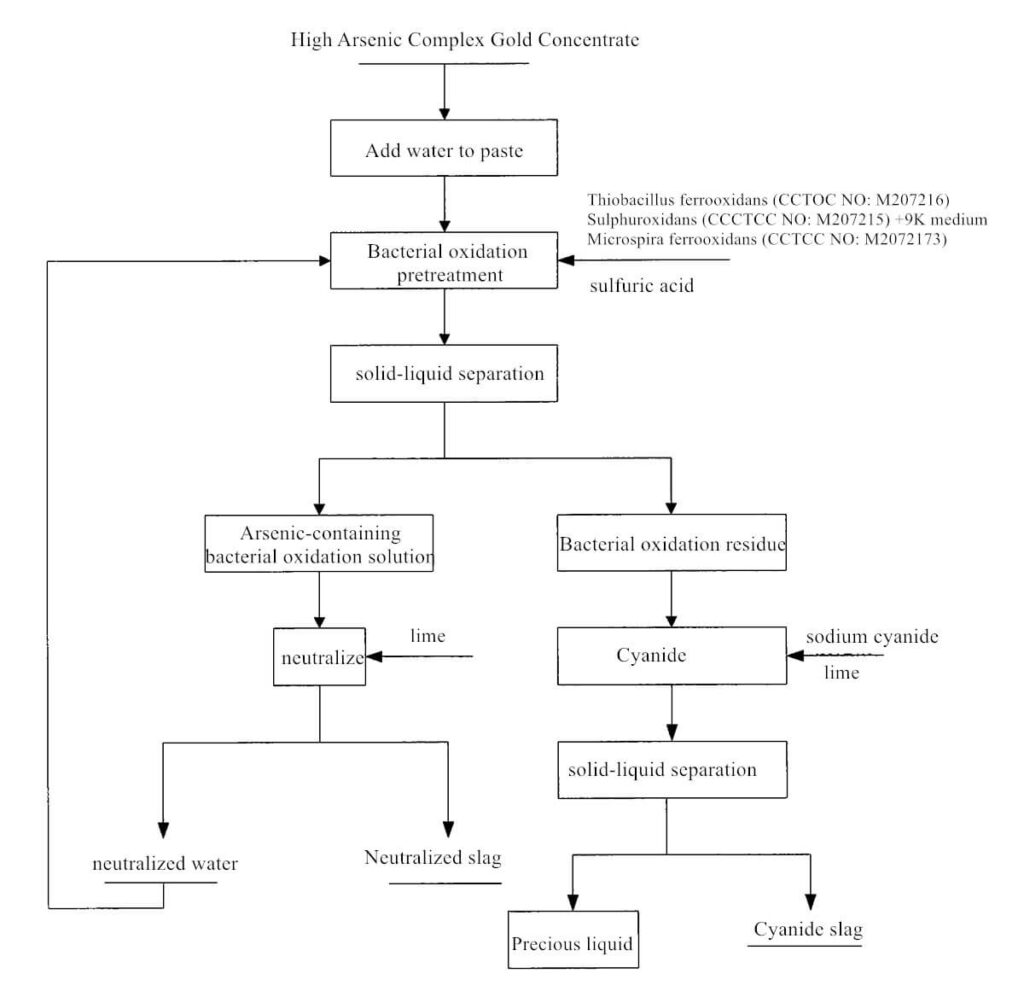
Bacterial Oxidation Pretreatment
The research on bacterial pre-oxidation is quite active. As early as the 1960s, the former Soviet Union discovered a new lytic autotrophic Thiobacillus ferric oxidant in the work of bacterial leaching of arsenic gold ore. They are using this arsenic-resistant bacteria to decompose Arsenopyrite and pyrite. It can dissociate Au encapsulated in it. The mechanism of action is the same as the process of pressurized oxidation, and bacteria play the role of catalytic oxidation. Under bacteria action, It can accelerate the decomposition and oxidation process of many minerals dozens or even hundreds of times. After leaching for 60-120 hours, the oxidation rate of Arsenopyrite can reach 80%-90%. The results of small-scale tests show that when the leaching residue applies cyanide treatment, it will increase the gold’s 30% – 50% leaching rate during cyanide after biological oxidation. Carry out the bacterial leaching under normal pressure at 25 to 35 °C, and use compressed air to supply oxygen to the pulp and stir to intensify the reaction process. It can roughly divide bacterial oxidation and gold extraction operations into:
- Cultivate Thiobacillus iron ferric in bacterial culture medium to prepare a sulfuric acid bacterial infusion with pH 1.5-2.5;
- Catalytic oxidation of bacteria to remove arsenic and sulfur;
- Pretreatment obtained The slag is then cyanided (or by other methods), and the gold extraction pretreatment solution is activated by bacteria and then reused.
The Institute of Microbiology, Chinese Academy of Sciences, has also done many years of work on bacterial oxidation. In 1980, the arsenic-gold concentrate de-arsenic test was carried out at Shangling Gold Mine in Pingguo, Guangxi. >1085 pieces/mL, stirring for 5 to 6 days and nights (or multi-stage leaching), washing the leaching residue with HCl, the removal rate of arsenic is about 90%, and the recovery rate of Au is >90%. Later, it conducted similar research in Karamay Gold Mine in Xinjiang and obtained good results. Recent studies on bacterial selection, culture and genetic reproduction, and the decomposition of arsenic-gold ore have made gratifying progress. The principle and process of bacterial oxidation showed that this method has the unique advantages of simple equipment and less consumption of reagents. Still, there are also disadvantages such as too long and no recovery of valuable elements such as As.
Gold leaching pretreatment is a necessary step in the gold mining process. By removing the impurities from the ore, gold leaching pretreatment allows for more efficient and cost-effective gold extraction. Besides roasting and bacterial oxidation pretreatments, there are also other pretreatments. If you want to know more, please follow our blog for updates.