According to different useful components, we can divide copper sulfide ore into the following categories:
- Single copper mine
The ore is relatively simple, and copper is the only valuable component. Gangue is mainly quartz, silicate, and carbonate. - Copper-sulfur ore
In addition to copper minerals, we can recover iron sulfide minerals from copper-sulfide ores. The main sulfur mineral is pyrite, which is why this ore is called copper-bearing pyrite. - Copper pyrite
In addition to copper minerals and pyrite that can be recycled, magnetite is also worth recycling in its ores. - Copper-molybdenum ore
In addition to copper minerals, the valuable components of copper molybdenite also contain molybdenite. In addition to copper and molybdenum, magnetite and pyrite can be recovered. - Copper-nickel ore
In addition to copper minerals, its useful ingredients also include nickel-containing minerals, such as nickel sulfide ore and nickel-containing pyrite, pyrrhotite, etc. - Copper and cobalt ore
In addition to copper minerals, its useful ingredients include pyrite containing cobalt, which is selected to become a cobalt concentrate.
Copper Sulfide Ore Flotation
Iron Sulfide Minerals in Copper Ores
All copper sulfide ores have iron-containing sulfides, so the flotation of copper sulfide ores is essentially the separation of copper sulfide and iron sulfide. Common iron sulfide minerals in copper ores include pyrite, pyrrhotite, and marcasite.
Pyrite
Pyrite (FeS2) contains S53.4%, is widely distributed in sulfide ores, and can be found in almost all mineral deposits. Since pyrite is the primary raw material used to make sulfuric acid, pyrite concentrate is often called sulfur concentrate.
Pyrite can use xanthate as a collector in acidic, neutral, and weakly alkaline slurries. Pyrite treated with acid (sulfuric acid, hydrochloric acid) has very good floatability (when using xanthate, pH=4.5 is best). In weakly alkaline slurries with pH=7~8, xanthate collection is also an industrially economical and effective method. The capturing power of pyrite is weaker than that of xanthate.
Pyrite inhibitors are cyanide and lime. Chalcopyrite, sphalerite, and pyrite separation mainly use lime as a pyrite inhibitor. The inhibited pyrite can be activated by lowering the pH with sulfuric acid, sodium carbonate, or carbon dioxide. Copper sulfate is often added during activation.
Pyrrhotite
Pyrrhotite (Fe5S6Fe16S17) generally has lower sulfur content than Pyrite. It is an iron sulfide mineral that is easy to oxidize, muddy, and relatively difficult to float.
Floating magnetic Pyrite in alkaline and weakly acidic slurries must first be activated with Cu2+ ions or a small amount of sodium sulfide and then collected with high-grade xanthate.
Inhibitors of pyrrhotite include lime, cyanide, and sodium carbonate. In exceptional cases, potassium permanganate can be used, such as when arsenopyrite or pentlandite is separated from pyrrhotite, potassium permanganate can be used to inhibit pyrrhotite, and copper sulfate or sodium sulfide can be used to activate arsenopyrite, nickel Pyrite.
When pyrrhotite oxidizes in the slurry, it consumes the oxygen. The oxygen in the slurry is vital for the flotation of sulfide ore. When there is pyrrhotite in the ore, xanthate is used to flotate other sulfide ores. Before oxygen reacts with pyrrhotite, other sulfide ores will not float, and only oxygen remains in the slurry, causing the surface of other sulfide ores to be partially oxidized to make them float. Therefore, when flotating sulfide ores containing pyrrhotite in the ore, it is essential to adjust the stirring and aeration of the slurry.
The activators of pyrrhotite include copper sulfate plus sodium sulfide, sodium fluorosilicate, and oxalic acid. Pyrrhotite is a large part of the sulfur-containing minerals in my country’s skarn-type copper deposits. Because pyrrhotite is not easy to float and has magnetic properties, it is mixed in magnetically separated iron concentrate, which is the main reason for the high sulfur content in iron concentrate.
Marcasite
Marcaite (FeS2) has the same chemical composition as Pyrite but with a different crystallization. Pyrite has an equiaxed crystal system, and marcasite has an orthorhombic crystal system.
The floatability of marcasite is similar to that of Pyrite but better than that of Pyrite.
The order of floatability of several iron sulfide ores collected with xanthate is marcasite > Pyrite> pyrrhotite.
Copper Sulfur Flotation Plant
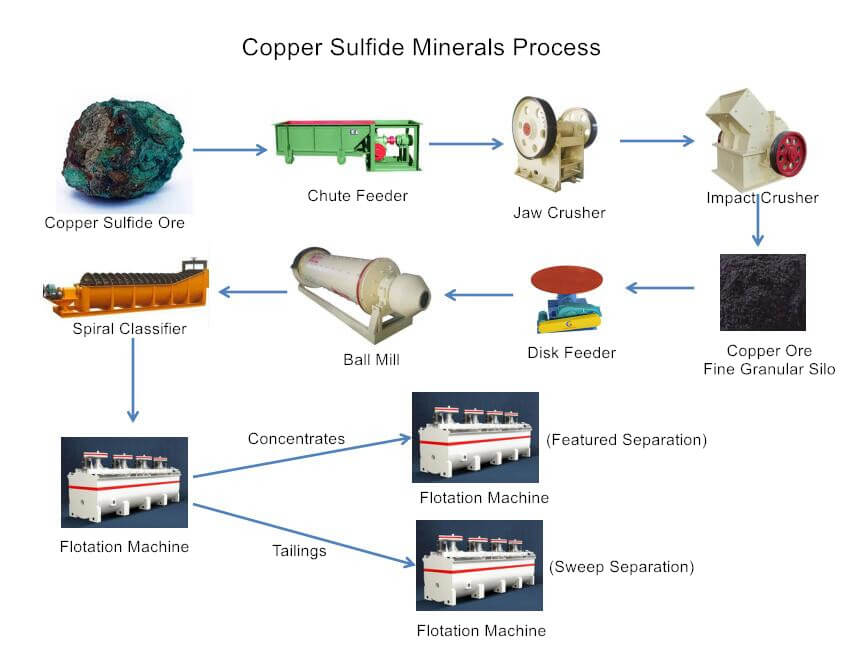
Flotation Process of Copper Sulfur Ore
1. Priority flotation
Generally, the copper is first, and then the sulfur is floated. The pyrite content in the ore is relatively high for massive copper-containing pyrite. High alkalinity (free CaO content >600~800g/m3) and high xanthate dosage are often used to suppress the pyrite by floating copper. The tailings are mainly pyrite and very few gangues, so the tailings are sulfur concentrates. A priority flotation process is adopted for disseminated copper-sulfur ores. The tailings after floating copper must be floated with sulfur again. To reduce sulfuric acid consumption during sulfur floating and ensure safe operation, low alkalinity process conditions should be used as much as possible when floating copper.
2. Mixing-separation flotation
This process is more advantageous for copper-sulfur ores where the raw ore contains low sulfur, and the copper minerals easily float. Copper and sulfur minerals are first mixed and floated in a weakly alkaline slurry. The mixed concentrate is added with lime to separate copper and sulfur in a highly alkaline slurry.
3. Semi-preferential mixing-separating flotation
Semi-preferential mixing-separation flotation uses Z-200, OSN-43, Ester-105, etc., with good selectivity as the collector for semi-preferential copper floating operations. The easily floating copper minerals are floated out first, and some qualified copper minerals are obtained. The copper concentrate is then subjected to copper-sulfur mixed flotation, and the resulting copper-sulfur mixed concentrate is subjected to separation flotation using copper floating and sulfur suppression. This separation process avoids the inhibition of effortlessly floating copper minerals under high lime dosage and does not require consuming large amounts of sulfuric acid to activate pyrite. Production practice shows that this process has reasonable structure, stable operation, good indicators, and the characteristics of recovering the target mineral as early as possible.
As far as the grinding and flotation process is concerned, for difficult-to-separate copper ores, it is more advantageous to adopt a staged grinding and flotation process, such as coarse concentrate regrinding and then separation, mixed concentrate regrinding and separation, medium ore regrinding and separate processing, etc., which domestic and foreign dressing plants widely used.