The ball mill is an important part of the mineral processing equipment. It is widely used in the production line configuration as an important part of mineral processing after grinding. The grindability of ore is a specific indicator to measure the resistance of ore to external forces, which measures the ability or difficulty of ore to be ground. The grindability of ore refers to the ability to be finely broken into a certain particle size under certain physical forces. It is an important parameter that determines the mineral processing process and equipment selection. The following editor will introduce you to the relevant knowledge of ore grindability in mineral processing.
1. What is Ore Grindability?
Ore grindability refers to the ability of a mineral sample to be ground to the lowest particle size during processing. For mineralogists and miners, ore grindability is an important indicator for evaluating the efficiency of mineral processing.
Generally, ore grindability can be determined by factors such as the crystal structure, composition, and distribution of the mineral. For different types of minerals, their grindability is also different. For example, copper ore is usually more grindable than quartz, while marble is usually less grindable than copper ore.
During ore processing, the grindability of the mineral sample can be adjusted by controlling the parameters of the mill, such as grinding force, output, grinding time, etc. In addition, the grindability of the ore can be improved by improving the ore pretreatment methods, such as acid washing, magnetic separation, flotation, etc.
2. Why is Grindability Important?
Grinding equipment is the key equipment of a mineral processing plant. The investment and operating costs of the grinding section account for a large proportion of the entire mineral processing plant. Whether the grinding fineness can meet the requirements is of decisive significance for whether the designed mineral processing plant can achieve the design indicators. Therefore, in the design of a mineral processing plant, the grindability of the ore is extremely important original data. Grindability is a crucial parameter in the mining and mineral processing industries for several reasons:
- Energy Efficiency
Grinding is one of the most energy-intensive processes in mineral processing. Knowing the grindability of an ore helps in estimating the energy requirements for grinding operations. This can lead to significant energy savings and cost reductions in the milling process. - Equipment Selection
Different types of ores require different grinding equipment. By understanding the grindability of an ore, engineers can select the most appropriate milling machinery and optimize its operation. This ensures that the equipment used is efficient and effective for the specific ore type. - Process Optimization
Accurate knowledge of grindability allows for the design of optimal grinding circuits. It aids in determining the best operating conditions (such as mill speed, load, and grinding media) to achieve the desired particle size distribution, enhancing the overall efficiency and throughput of the milling process. - Product Quality
The fineness of the ground ore is critical for the subsequent processing steps, such as flotation, leaching, or magnetic separation. Proper grindability assessment ensures that the ore is ground to the appropriate size, improving the recovery rates and quality of the final product. - Economic Evaluation
Grindability affects the cost of comminution, which is a significant portion of the overall operating costs in mining operations. By accurately assessing grindability, mining companies can better predict the costs associated with grinding and make more informed decisions regarding project feasibility and profitability. - Environmental Impact
Efficient grinding processes reduce energy consumption and greenhouse gas emissions associated with mining operations. Understanding and optimizing grindability contributes to more sustainable and environmentally friendly mining practices. - Safety and Maintenance
Properly assessing grindability helps in predicting wear rates and the lifespan of grinding equipment. This leads to better maintenance planning, reduced downtime, and safer operation conditions.
Ore grindability is of great significance for mineralogical research and industrial processing. It can not only determine the mineral composition and distribution but also measure the processing capacity and production efficiency of the ore. Therefore, in the fields of mining, processing, and scientific research, it is crucial to understand the grindability of the ore.
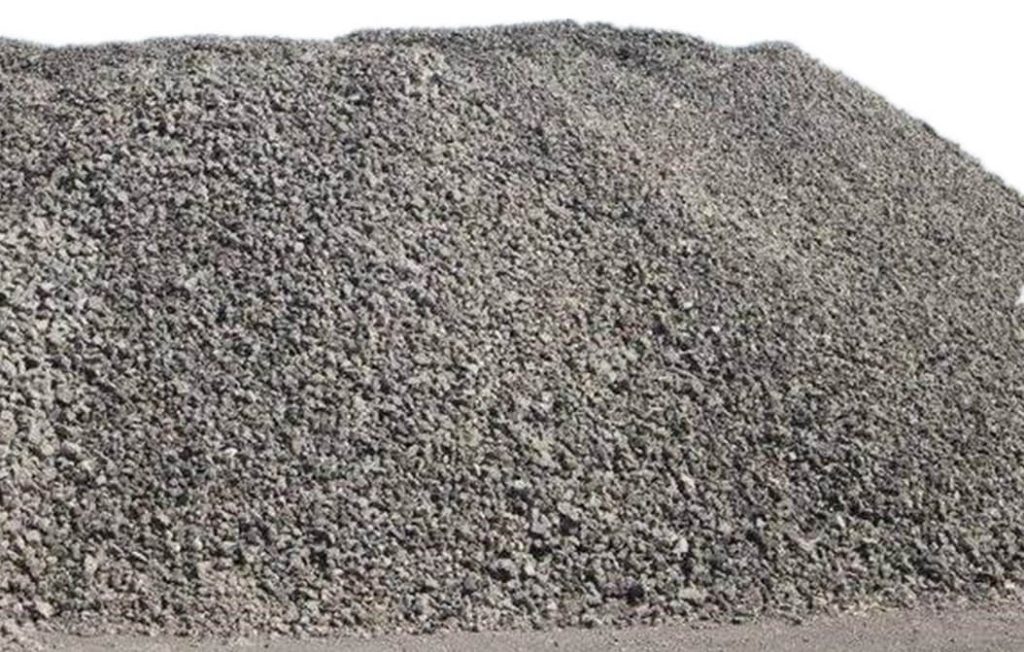
3. How to Test Ore Grindability?
Testing ore grindability involves several standardized methods, each designed to measure specific aspects of the grinding process. Here are some of the most common tests used to assess ore grindability:
- Bond grindability test
This test is one of the most widely used methods for determining grindability. The principle is to put a standard-sized spherical steel ball into a standard-sized screen, then put it into a cylinder filled with a certain weight of steel balls and water, perform rotational friction, and finally classify through the screen and calculate the average value. - JK industrial test
This test is similar to the Bond grindability test, but more parameters are added during the experiment, and the results are calculated and analyzed more accurately. - SPI (SAG Power Index) Test
Procedure: Measures the time required to grind a specific amount of ore in a small semi-autogenous grinding (SAG) mill.
Outcome: The SPI value helps in designing SAG mill circuits and predicting their performance.
Standard: Conducted according to methods developed by Starkey & Associates. - Other Test
There are other methods for determining grindability, such as the SMC test, which is less commonly used.
4. What Factors Affect The Grindability of Ore?
Factors affecting the grindability of ore
- Mineral composition: Different types and grades of minerals have different compositions and their hardness will also vary. Aggregates with high hardness are difficult to be crushed into smaller particles.
- Mineral crystallinity: The higher the mineral crystallinity, the greater its hardness and the more difficult it is to be crushed.
- Mineral particle size: The larger the particle, the greater its hardness and the more difficult it is to be crushed.
- Impurities in minerals: Impurities in minerals such as quartz, calcite, and other impurities with higher hardness will affect grindability.
- Mill type: Different types of mills have different adaptability to different types and hardness of ores. Therefore, grindability factors need to be considered when selecting.
Ore grindability is one of the important parameters for mineral processing and equipment selection. There are many methods to determine grindability, among which the Bond industrial test and J industrial test are currently the most widely used methods. Factors affecting grindability include mineral composition, crystallinity, particle size, impurities, and mill type. When determining the mineral processing and equipment selection, it is necessary to consider the grindability of the raw materials and select suitable processes and equipment to improve production efficiency and reduce energy consumption.