The flotation machine is used for mineral processing. The ore slurry is doped, stirred, aerated, and mineralized through a preprocessor so that some of the mineral particles are selectively fixed on the bubbles; they float to the surface of the slurry and are scraped out to form foam products. It is retained in the slurry to separate minerals. Flotation machines separate valuable minerals from waste rock or gangue.
Flotation Machine Components
The components of a typical flotation machine may vary slightly depending on the design and manufacturer, but here are the main components commonly found in most flotation machines:
Pulp and Froth Handling Mechanisms: Pulp and froth handling mechanisms include paddles, impellers, or rotors that agitate the pulp and create bubbles for mineral attachment. Motors typically drive them and are responsible for mixing the pulp and dispersing air bubbles throughout the pulp.
Agitator: The agitator stirs the pulp to ensure the proper mixing of reagents, minerals, and water.
Air Distribution System: This system introduces air into the flotation cell. It may include air spargers, pipes, or tubes that release air bubbles into the pulp.
Froth Removal System: Once the valuable minerals are attached to the air bubbles, they form a froth layer at the top of the flotation cell. A mechanism for removing this froth is essential. Common methods include mechanical paddles, overflow weirs, or skimmers.
Launders: Launders are troughs located at the top of the flotation cell. They collect the froth and direct it to the froth removal system.
Pulp Level Control System: This system ensures that the pulp level inside the flotation cell remains within the optimal range for efficient operation. It may include sensors, valves, and control mechanisms.
Reagent Dispensing System: Flotation often requires the addition of chemical reagents to promote selective attachment of minerals to air bubbles. A reagent dispensing system accurately doses these chemicals into the flotation cell.
Instrumentation and Control System: Modern flotation machines often include sophisticated instrumentation and control systems to monitor and regulate parameters such as pulp level, air flow rate, froth depth, and reagent dosage.
Drive Assembly: Flotation machines are typically powered by electric motors or other prime movers. The drive assembly transmits power from the motor to the agitator or impeller.
Support Structure: A robust support structure is necessary to house and support all the components of the flotation machine.
These components work together to separate valuable minerals from gangue materials in the flotation process.
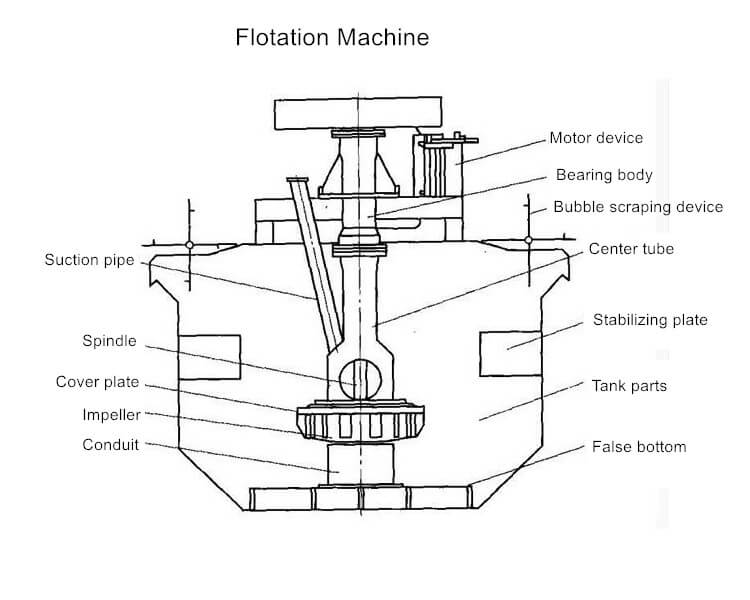
Functions of Each Component of The Flotation Machine
Air source device
The air source device is the core component of the flotation machine and a key component of bubble separation. It usually consists of a gas tank, a pressure gauge, a throttle valve, and a flat air pipe. Its primary function is to provide compressed air into the flotation tank to form many small bubbles so that the mineral particles and foam can be combined to separate minerals and non-mineral substances. At the same time, the air source device can also control the bubble size and flotation effect.
Stirring device
The stirring device is another critical component of the flotation machine. Its function is to maintain sufficient stirring of the slurry in the rotating flotation tank so that the mineral particles can fully interact with the foam, thereby improving the flotation effect. Usually, the stirring device includes a motor, reducer, impeller, and slurry mixer.
Foam tank
The foam tank is the foaming and separation part of the flotation machine. Its function is to use the bubbles provided by the air source device to lift the un-floated mineral particles from the bottom of the tank to the tank surface and float from the top with the flotation foam discharge to achieve separation of minerals and non-minerals. The foam tank usually consists of a foam tank body, an outlet pipe, and a garbage chute.
Overflow tank
The overflow tank is a device in the flotation machine that regulates the slurry flow. It adjusts the slurry diversion ratio between the inlet and outlet and the foam tank, achieves stable slurry inlet and outlet flow, and maintains the pressure and other parameters of the flotation foam height and gas in the flotation machine. It usually consists of an overflow tank and an optimized structural plate.
Tank body
The tank is the main part of the entire flotation machine, usually divided into a rotating flotation tank and a static flotation tank. The rotary flotation tank mixes the slurry and bubbles through the stirring equipment, allowing the mineral particles to interact with the foam to achieve purification and separation; the static flotation tank uses the tank’s structural design to reduce vortex and mixing as much as possible so that the bubbles can adequately interact with mineral particles to achieve separation.
The various components of the flotation machine constitute the critical equipment for mineral separation. For example, the stirrer ensures that the mineral particles and bubbles in the suspension are fully mixed, the bubble introduction system promotes effective contact between the mineral particles and the bubbles, the scum removal system removes the bubbles containing the target mineral from the suspension, and the suspension circulation system To ensure sufficient circulation of the suspension, the control system monitors and adjusts operating parameters to optimize the separation effect. The agent addition system adjusts the chemical properties of the suspension. The synergistic effect of these components enables the flotation machine to efficiently separate minerals, providing a fundamental guarantee for ore extraction and processing.
JXSC Mineral has an inseparable relationship with flotation machines as a manufacturer specializing in producing mining equipment. Its profound technical accumulation and rich industry experience have made it one of the leaders in flotation machines. JXSC is committed to developing and producing high-quality, high-efficiency flotation machines and constantly promotes the innovation and development of flotation technology to meet the needs of the global mining market. Its professional team continuously improves and optimizes the design and performance of flotation machines to provide reliable solutions for mineral separation. The indissoluble bond between JXSC and flotation machines is that it is not only a manufacturer of flotation machines but also an advocate and leader of flotation technology, committed to bringing more innovations and breakthroughs to the global mining field.