Flotation is a technique widely used in mineral processing to separate valuable minerals from gangue or waste materials. The process involves introducing air bubbles into a slurry consisting of finely ground ore and water. The air bubbles attach to the hydrophobic particles and bring them to the surface for easy collection. There are two main types of flotation equipment: flotation cells(machines) and flotation columns.
Flotation Machines/Cells
A flotation cell/machine is a common and widely used flotation equipment consisting of a series of tanks or chambers connected by pipes and valves. Slurry and air are fed into the first flotation cell where it is mixed with reagents, which form bubbles and rise to the top, forming a froth layer. The froth is then skimmed off and transferred to the next flotation cell for further cleaning and enrichment. This process is repeated until the desired grade and recovery is achieved. Flotation cells can be designed in different ways depending on the size, shape, and mineralogy of the ore and the desired product quality.
Flotation Columns
The flotation column was invented in the 1960s. Its unique structure and movement made it popular in many coal preparation plants and ore dressing plants in many countries from the beginning. However, due to the unreasonable structure and unstable movement of the early flotation column, its development was slow. In recent years, with in-depth research on the flotation column, several flotation columns with their characteristics have been developed with the bubble generator as a breakthrough. These flotation columns have greatly improved the reliability of the equipment and the stability of operation compared with the early flotation columns.
The flotation column is a newer and more advanced type of flotation equipment consisting of a tall, narrow cylindrical vessel with an ejector at the bottom. The slurry is fed into the column from the top and flows downward by gravity, countercurrent to the rising bubbles. These bubbles attach to the hydrophobic particles and carry them to the top where a froth layer is formed. The froth is then removed by a washer or froth squeezer and collected as concentrate. The slurry that reaches the bottom of the column is discharged as tailings. Flotation columns can be used as stand-alone units or in conjunction with flotation cells, depending on the application, ore characteristics and process goals.
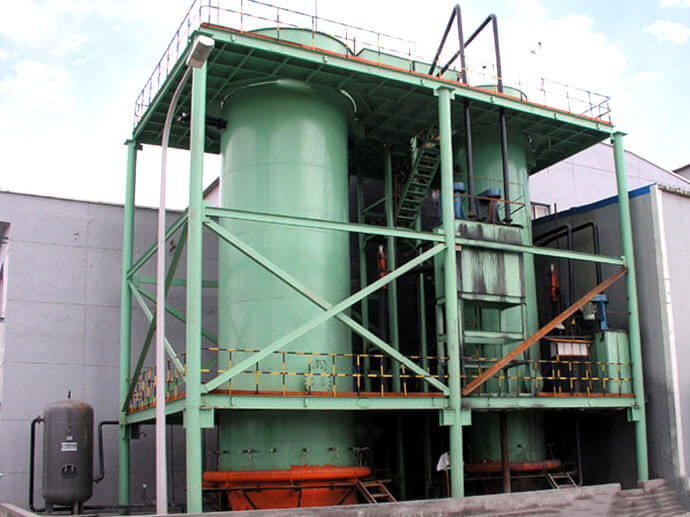
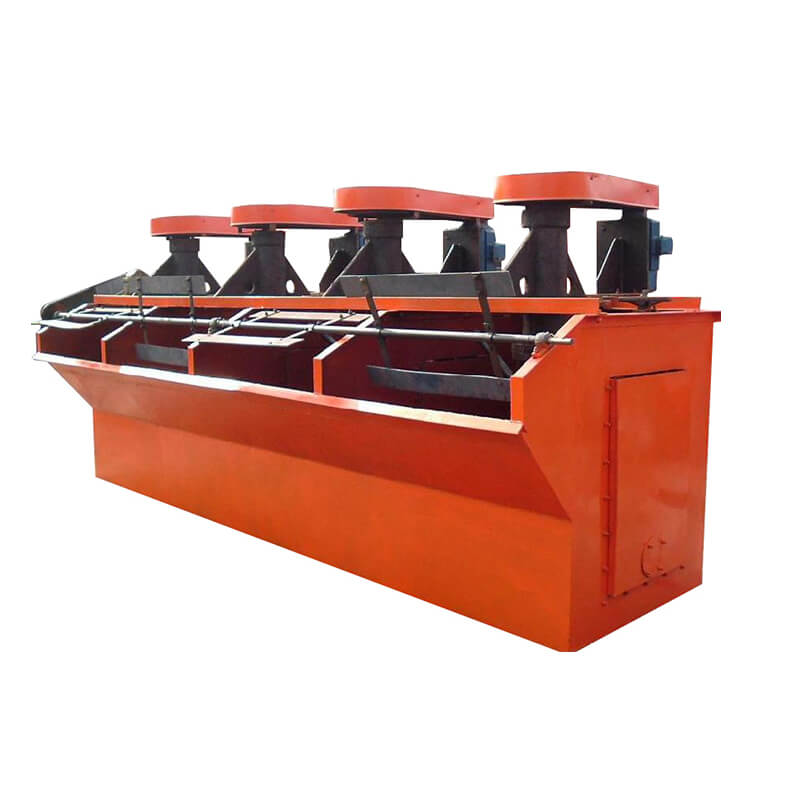
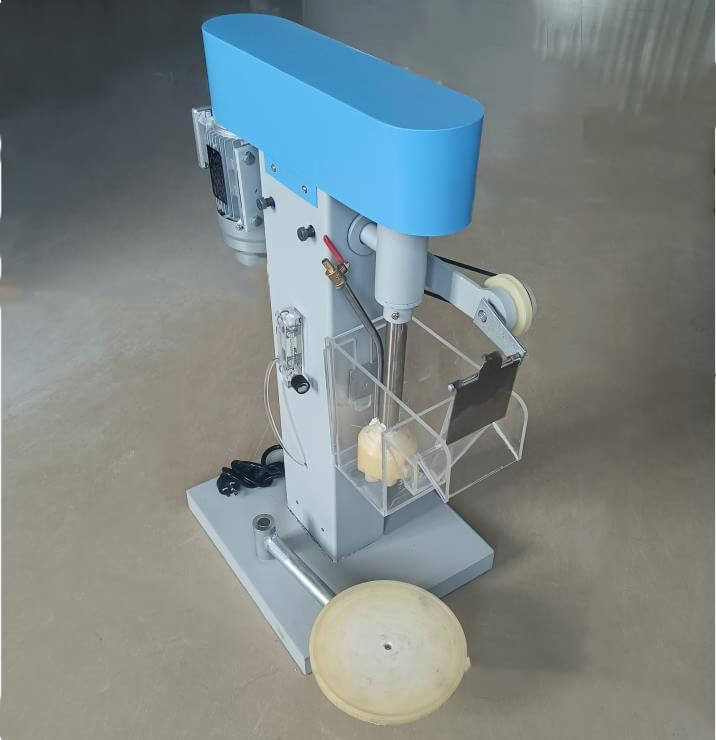
Flotation Columns VS Flotation Machines: The Differences
Flotation columns and flotation machines are both used in mineral processing to recover valuable minerals from raw materials. Flotation columns are a type of flotation machine, and they differ from other types in several ways:
- Mechanical agitation
Flotation columns don’t use mechanical agitation or shear, while other types of flotation machines do. - Cell shape
Flotation columns are tall, narrow, cylindrical vessels, while other flotation cells can be rectangular. - Gas bubbles
Flotation columns use compressed air to create bubbles through sparging, while other flotation cells use agitation. - Mixing
In flotation columns, the rising bubbles create turbulence that mixes the slurry. - Froth
Flotation columns produce deeper froths, and wash water is often applied to the froth’s surface. - Energy consumption
Flotation columns are more energy-efficient than other types of flotation machines.
Flotation Columns VS Flotation Machines: Separation Process
Conventional Flotation Machine Separation Process
The conventional flotation process sends the coal slurry water processed through the slurry pre-processor to the flotation machine. Filter the clean coal separated by the flotation machine by a disc vacuum filter.
The process is relatively complicated, especially since the vacuum filter must be equipped with vacuum pumps, gas-water separators, filtrate pumps, cooling water systems, softening water devices, and other equipment. In addition, the process generally requires 2 to 3 floors, and the civil engineering costs are relatively high. Therefore, the characteristics of this process are large investment, equipment, high power consumption, complex process, large maintenance, and high operating costs.
Since this process has been used in China for many years and has accumulated rich experience, it is currently the most widely used flotation process in China.
Flotation Column- Chamber Filter Press New Sorting Process
The flotation column-chamber filter press flotation process is a new coal slime flotation process system developed by the China University of Mining and Technology with a cyclone-static microbubble flotation column as the core. This process adopts a direct flotation process. The coal slime water is sent to the flotation column for sorting after slurry adjustment in the stirring tank, and the sorted clean coal is filtered by the chamber filter press. Compared with the previous process, this process is much simpler, with less investment, less power consumption, less maintenance, and low operating costs. At the same time, due to the inherent advantages of the flotation column, the adaptability, sorting accuracy and yield of this process to coal slime are higher than those of conventional flotation machines. In addition, this process makes full use of the advantages of the high discharge port of the flotation column and adopts a ground layout, which greatly saves civil engineering investment.
Flotation Columns VS Flotation Machines: Advantages & Disadvantages
Using flotation cells offers several advantages, such as the ability to handle a wide range of feed sizes and ore types, can be adjusted and optimized by changing operating parameters, achieve high throughput and recovery, and good selectivity and separation efficiency. In addition, they are relatively simple to operate and maintain. On the other hand, flotation columns also present several disadvantages, including the need for a large footprint and energy consumption, the generation of tailings and wastewater that require proper treatment and disposal, being affected by changes in feed characteristics, which degrades performance and stability, and the generation of turbulence and shear forces that damage bubbles and particles.
Advantages of using flotation columns include higher selectivity and separation efficiency, improved product quality and grade, reduced energy consumption and environmental impact, and easy scale-up and integration with existing flotation circuits. However, flotation columns also present several disadvantages, including greater difficulty in design, installation, and operation; less flexibility to changes in operating conditions; lower throughput and recovery; and the need for more instrumentation and control systems. In addition, skilled personnel and maintenance staff are required to ensure optimal performance and reliability of the flotation process.
Both flotation cells and columns have their advantages and disadvantages, depending on the application, ore characteristics, and process requirements. Understanding the difference between flotation cells and flotation columns can help you choose the best option for your mineral processing laboratory.