As a kind of crushing equipment, Roll Crusher is widely used in medium and fine crushing operations of high hardness materials in the chemical industry, metallurgy, building materials, refractory materials, and other industrial sectors, which is characterized by low noise, less dust, stable performance, and easy maintenance. Its capacity, i.e. the ability to process materials per unit of time, is one of the important indexes to measure its performance. Understanding and mastering the factors affecting the roll crusher capacity is significant for improving production efficiency and optimizing equipment configuration.
4 Factors Governing Roll Crusher Capacity
The capacity of the roll crusher is affected by many factors, mainly including the design parameters of the equipment itself, material characteristics, production environment, and operation mode. Design parameters such as roll diameter, roll spacing, and motor power directly determine the capacity of the equipment. Material characteristics include hardness, particle size, humidity, etc. These characteristics will affect the crushing difficulty and speed. The production environment and operation mode will also impact the capacity, such as whether the feed is even and the outlet is adjusted correctly.
Design Parameters
- Model size:The larger the roll diameter, the stronger the crushing capacity. The feed size of the mobile roll is related to the roll diameter of the roll crusher. The feed size determines the friction coefficient between the crushed materials. Usually, the ratio of the diameter of the tooth surface or tooth groove of the roll crusher rotor to the feed size is 2:6. The particle size is also related to the model of the roll crusher; the bigger the model, the more feed, the bigger the output, and the bigger the change of the material particle size. For example, the processing capacity of the 2PG1280 model is 30t/h-250t/h, while the processing capacity of the 2PG1212 model is 40t/h-350t/h.
- Roller surface and roller pitch: The adjustment of the roller pitch will affect the discharge particle size and processing speed;
- Motor power:The higher the motor power, the more stable the equipment operation is and the stronger the processing capacity.
Roll crushers use the process of timely roll spacing adjustment to ensure crushing quality. The roll surface of the crusher wears out quickly due to the generation of indentations, and the wear is uneven, requiring regular turning of the roll surface.
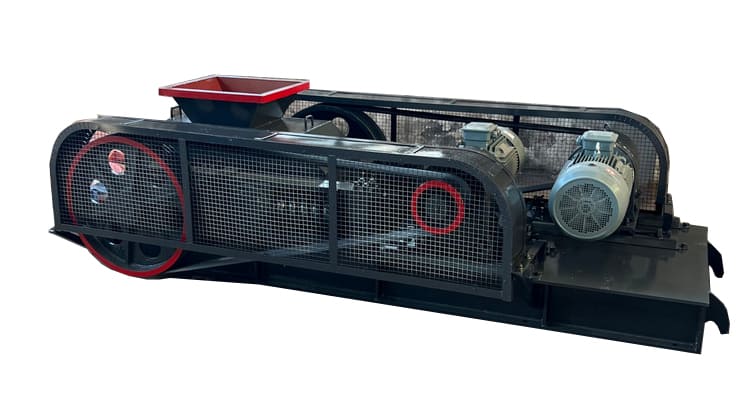
Material Characteristics
- Material hardness: The compressive strength of the material affects the processing capacity of the roll crusher; the higher the hardness of the material, the more serious the wear and tear of the roll crusher, the slower the crushing speed, and the smaller the processing capacity. The compressive strength of the materials the roller crusher can process is less than 160MPa.
- Particle size of material: There is a specific range of feed size for roll crushers, and the particle size of material directly affects its processing capacity. The larger the particle size of the material, the larger the selected model. Choosing a small crusher affects not only the quality of the crusher but also its output because the upper roll of a small crusher can’t bite the big pieces, which not only wears the roll skin but also causes the quality of the product and the output to drop. At present, the method of surfacing strip carbide along the length of the upper roll to improve the upper limit of the particle size of the crushed fuel has achieved certain results.
- Humidity and viscosity of the material: The moisture and viscosity of the material significantly impact the roll breaker’s processing capacity. When the moisture content of the material is large, the material is easy to adhere to the crusher, leading to clogging and reducing the processing capacity; high viscosity of the material is more likely to adhere, affecting the crushing effect. When the material is especially wet, it reduces the crushing quality and output and requires an appropriate reduction of feeding quantity. Usually, the moisture content of the material is not more than 30%.
The higher the hardness of the material, the more difficult it is to crush, and the capacity may be reduced; the larger the particle size, the more crushing time is needed, and the capacity will be affected; materials with high humidity may lead to sticking in the crushing process, affecting the capacity.
Production Environment
Feeding quantity and uniformity: Feeding quantity and uniformity of feeding have an important impact on processing capacity. Uneven feeding will lead to fluctuations in production, so choosing the right feeding equipment and controlling the uniformity of feeding is the key to improving processing capacity.
Uneven feeding may lead to unstable equipment operation, affecting the capacity; improper adjustment of the outlet may lead to material clogging or over-crushing, affecting the capacity.
Operation Mode
Equipment Maintenance and Parts Wear Resistance: The equipment’s maintenance condition and the parts’ wear resistance will also affect the processing capacity. Regular maintenance and replacement of worn parts can prolong equipment life and increase capacity.
Correct operation can ensure that the equipment operates in the best condition and increases the capacity; irregular operation may damage the equipment and reduce the capacity.
In summary, the capacity of a roll crusher is affected by many factors. Not only related to its quality and standard operation but also closely related to the material particle size, material moisture, roll surface and roll distance, feed speed, and uniformity, grasp the factors affecting the size of the output of the roll crusher, you can take corresponding measures to avoid in the operation process. Such as through a reasonable choice of equipment specifications, optimizing the production process, regular maintenance and repair, applying frequency conversion technology and energy recovery, and other measures that can effectively improve the capacity of the roller crusher to achieve the goal of energy-efficient production. Implementing these measures will help enterprises safeguard production efficiency while actively responding to energy conservation and emission reduction policy requirements and promote sustainable development.