The ball mill is the key equipment for crushing materials after they are crushed. It is widely loved by people in mineral processing, building materials, chemical, and other industries because of its characteristics of high efficiency, energy saving, intelligence, environmental protection, low carbon, durability, and long life.
Factors Affect The Output and Quality of Ball Mills
Many factors affect the output and quality of ball mills, which can generally be divided into three categories: process, mechanical, and management. From the perspective of production technology, the influencing factors are mainly the following 10 points:
1. Particle size of grinding materials
The grinding materials’ particle size affects the ball mill’s output and quality. If the particle size is small, the production and quality of the mill will be high, and the power consumption will be low; if the particle size is large, the output and quality of the mill will be low, and the power consumption will be high.
2. Easily grindable material
The grindability of materials refers to the difficulty of grinding the materials. The national standard stipulates that the grinding work index Wi (kwh/t) is used to express it. The smaller the value, the easier the material is to grind, and vice versa.
3. Moisture content of grinding materials
Ball mill grinding can be divided into two methods: dry grinding and wet grinding. For the dry grinding method, the grinding materials’ moisture content greatly influences the mill’s production and quality. The higher the moisture content of the grinding materials, the easier it is to cause saturation. Grinding or paste grinding reduces the grinding efficiency and lowers the mill output. Therefore, materials with large moisture content must be dried before being put into the grinding mill.
4. Temperature of the grinding material
If the temperature of the materials entering the grinding machine is too high, coupled with the impact friction of the grinding body, the temperature inside the grinding mill will be excessive, and ball sticking will occur, reducing the grinding efficiency and affecting the mill’s output. At the same time, the thermal expansion of the mill cylinder affects the mill’s long-term safe operation. Therefore, the temperature of the grinding materials must be strictly controlled.
5. Fineness requirements of grinding materials
The finer the required fineness of the grinding material, the lower the output. On the contrary, the higher the output. For some fields, overemphasis on fineness must be consistent with economic production requirements. For example, in the cement industry, actual production shows that when the product fineness is 5 to 10%, the output decreases by 5% for every 2% decrease in fineness. When the fineness is controlled below 5%, the mill output decreases even more. Therefore, choosing the appropriate product fineness is also essential in improving the production and quality of ball mills.
6. Grinding process
For ball mills of the exact specifications, the output of the closed-circuit process is 15 to 20% higher than that of the open-circuit process. During closed-circuit operation, choosing the appropriate powder selection efficiency and cycle load rate is essential in increasing the mill’s output.
7. Powder selection efficiency
The powder selection efficiency of a closed-circuit mill greatly influences the output of the mill. Generally speaking, the powder separator’s efficiency is high and can improve the grinding efficiency of the mill. However, the powder separator itself cannot perform the grinding function, so the function of the powder selector must be coordinated with the grinding function of the mill to increase the mill’s output. Production practice has proved that the efficiency of the first-level closed-circuit long grinding powder separator is generally controlled at 50~80%. The optimal powder selection efficiency needs to be determined through multiple experiments.
8. Cycle load rate
The cycle load rate refers to the ratio of powder returned by the powder separator (i.e., coarse powder) to the amount of finished product. In order to improve the grinding efficiency of the mill and reduce the phenomenon of over-grinding in the mill, the cycle load rate should be appropriately increased. However, if the cycle load rate is increased very high, too much material will be in the mill, reducing the grinding efficiency.
9. Add grinding aids
Some grinding aids will affect the grinding effect because the most commonly used grinding aids are organic substances with strong surface activity. During the material grinding process, they can be adsorbed on the material’s surface, accelerate the crack expansion during material crushing, and reduce the occurrence of fine powder. The mutual bonding between them improves grinding efficiency and is conducive to energy savings and high productivity of the ball mill.
10. Ball-to-material ratio
The ball-to-material ratio is the ratio between the grinding body’s mass and the material’s mass. If the ball-to-material ratio is too large, it will increase the wasted work loss due to impact friction between the grinding body and the lining plate, increase power consumption, and reduce output. Choosing the ball loading amount and the ball-to-material ratio of the ball mill is the most common problem in actual production.
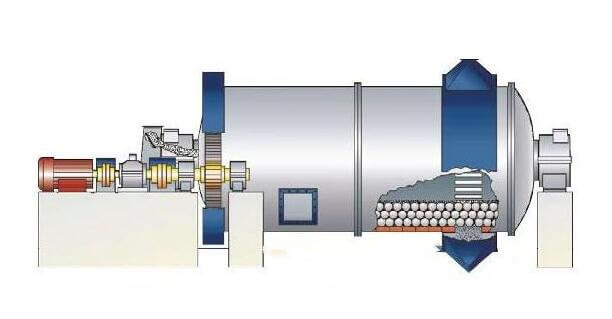
In addition to process factors, the model and parameters of the ball mill and the work of production, repair, and maintenance personnel also affect the production and quality of the ball mill. The energy-saving and high production of the ball mill is a systematic project. Each link is interconnected and restricts each other. The best energy saving and high production results can be achieved only through comprehensive consideration and close cooperation.
How to Increase The Production Capacity of The Ball Mill?
1. The technical content of the ball mill must be high.
The technological content of a ball mill not only affects its price but also affects its production capacity. Ball mills are updated relatively quickly, and only with high technical content can they achieve better production and increase production capacity.
2. The overall performance of the ball mill should be better.
Improving the production capacity of a ball mill requires excellent quality, advanced technology, and overall performance, which significantly impacts its production efficiency. If the structural design of the ball mill is unreasonable, the operation is unstable. The safety factor is low, the service life is short, etc., and these will inevitably affect the continuous production of the ball mill. Therefore, the overall performance of the ball mill is better.
3. The ball mill is of good quality.
The better the quality of the ball mill, the more stable the performance of the ball mill will be during operation. In addition, as for the lining plate of the ball mill’s wearing parts, the quality of the lining plate affects the overall production efficiency of the ball mill. As we all know, the lining plate of the ball mill is a wearing part. If the quality of the lining plate cannot be guaranteed, it will need to be replaced in time once it wears out, which will increase the cost and affect production. In addition, the grinding medium of the ball mill grinds materials through gravity. Suppose the quality of the steel balls is not up to par. In that case, it will inevitably affect the user’s normal production, reduce the ball mill’s production efficiency, and reduce its production capacity.