Quartz sand ball mill is the key equipment for crushing materials after they are crushed, applicable to quartz sand purification, non-metallic mineral processing and glass ceramics and other industries. It can be dry or wet grinding of various ores and other grindable materials. How do you choose dry grinding and wet grinding materials when choosing ball mill grinding materials? Follow me and read below and you will find the answer.
What is Dry Grinding and Wet Grinding?
Dry Grinding
Dry grinding refers to when the quartz ore in the ball mill after a certain crushing operation, in order to meet the requirements will be to the cylinder outside of the airflow to bring out. The ball mill used in the dry grinding process is a dry ball mill, dry ball mill production process without adding water, the requirement of the material must be dry, so it is known as dry grinding, the equipment is a straight cylinder, with the induced draft device, dust exhaust pipe, and dust collector. It plays an important role in “grinding” in the production of various minerals for beneficiation.
Wet Grinding
Wet grinding refers to the quartz ore being in the mill, in the grinding media, and the interaction of the ore itself to complete a certain amount of grinding, and to meet the user’s grinding needs, at the same time in the process will also be involved in the flow of water, the movement of the ore is required to be driven by the flow of water. The wet grinding process used in the ball mill is a wet ball mill, according to the movement characteristics, divided into simple swing-type wet ball mill, complex swing type wet ball mill, and mixed swing-type wet ball mill three forms.
What’s The Difference Between Dry And Wet Grinding?
Structure
The basic structure of the dry and wet ball mill is almost the same, which consists of a feeding, discharge port, rotary body, transmission part(reducer, small transmission gear, motor, electric control), and other main parts. The difference between the wet and dry ball mill is: that the dry ball mill outlet is a straight cylinder, but also installed air-induced device, dust; wet ball mill outlet is flared, built-in spiral device, easy to discharge material. Most of the ball mills on the market are wet ball mills, which have high grinding fineness and a good beneficiation effect.
Working Principle
A dry ball mill is a cylindrical rotating device, a gear drive along the outer edge, two bins, lattice type ball mill. Materials from the feeding device through the feeding hollow shaft spiral evenly into the first warehouse, the warehouse has a stepped liner or corrugated liner, filled with different specifications of the steel ball, the cylinder rotation generates centrifugal force that will bring the steel ball to a certain height and then fall, the material to produce heavy impact and grinding effect. After the material reaches rough grinding in the first warehouse, it enters into the second warehouse through the single-layer partition board, which is set with flat lining board and steel balls inside, and further grinds the material. The powder is discharged through the discharging grate plate to complete the grinding operation.
The working principle of the wet ball mill is the same as the dry grinding method, that is, it is necessary to add liquid media in the grinding process, and attention must be paid to the proper control of grinding concentration. The amount of water added is generally based on the use of mud, the amount of clay in the formula, and the size of the clay water absorption value. The material is gradually crushed under the impact and grinding effect. The crushed ore is discharged out of the cylinder through the discharge part. The discharged minerals are classified into qualified products in the spiral classifier, and the coarse sand is returned to the ball mill through the combined feeder to continue grinding. The feeding machine feeds continuously and evenly, the ore enters the ball mill continuously and evenly through the joint feeder, and the crushed materials are discharged from the ball mill continuously.
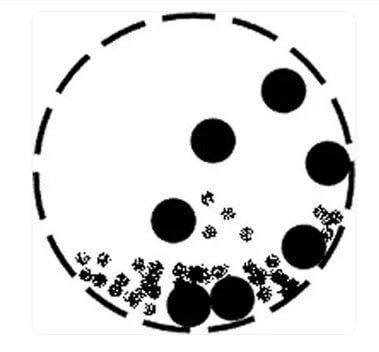
Applicable Conditions
Dry grinding, due to the design of the cylinder, sometimes forms a dead end, in the dead end of the part of the material is not ball milling; but wet grinding and dry grinding compared to also have a weakness, that is, wet grinding powder to dry to remove moisture or other liquid media, so it will increase the energy consumption and cost; cement can not be used in wet grinding. So both have their characteristics, according to the need to choose the appropriate grinding method in the material grinding.
Advantages
Advantages of dry ball mill
- Dry ball mill adopts grate plate mill tail discharge, smooth discharge, no rising grinding phenomenon, the cylinder does not need to be cooled, long service life, and low failure rate.
- Dry ball mill auxiliary equipment, change the original mill structure, make the body, chassis integration, installation can be lifted on the foundation plane, the spindle bearings with double-row centripetal spherical roller bearings, can reduce energy consumption by 30%.
Advantages of wet ball mill
- Wet ball mill performance is superior, and grinding efficiency is higher, the requirement of ore moisture content is low, and it can deal with ores with high moisture and mud content.
- Wet ball mill auxiliary equipment is less expensive, and the material transportation device is simple, so the investment is about 5%-10% lower than dry ball mill.
- Wet ball mills can not only make agglomerates ball mills into fine particles (but rarely split particles) – round particles, but also can force barren materials and plastic materials to stir and mix evenly.
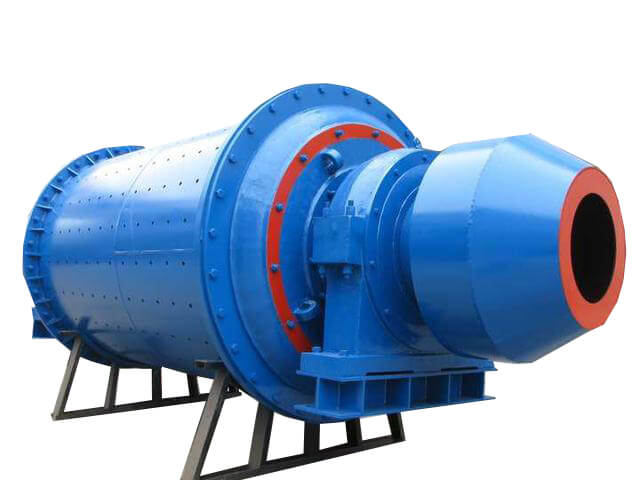
How to Choose Between Dry and Wet Ball Mill?
Correct choice of dry or wet grinding feeding method
Whether the material is fed dry or wet depends entirely on the subsequent operations in the ball mill and the nature of the product. Some materials need dry grinding because such materials in addition to water will produce physical or chemical changes. And materials in the ball mill in the fine grine grains in the product are larger, which in some cases, may be the people need to grind. Only to find the material adapted to the grinding method, to ensure that the ball mill quality and end process, dry grinding on the liner and media wear is relatively small, while the proportion of efficient operation, the two types of mill equipment have their advantages, according to the specific circumstances of the correct choice of dry grinding wet grinding to the way.
Wet grinding economy, more commonly used than dry grinding
From the point of view of the overall economic effect of the ball mill grinding operations, mineral processing will generally use wet grinding. Wet ball mill because it has a strong adaptability to the material, continuous production, crushing ratio, easy to adjust the speed of the fineness of the ground product, and other advantages, the application is also the most widely used. Wet ball mill discharge is a flared, built-in spiral device, convenient for discharging material. Most of the ball mills sold on the market are wet ball mills, wet ball mills have high grinding fineness and good beneficiation effect.
Considerations in the selection of dry and wet grinding process
- When the particle size of the powder is not required to be very fine or ball milled products need to be stored or sold in powder form (such as glaze, pigment grinding), as well as products such as bricks and other products pressure molding, the use of dry milling process is appropriate. For example, in the production of cement, one must choose dry grinding, not wet grinding, otherwise, it will be difficult to meet the needs.
- For dry grinding, generally, the liquid medium in the material does not react, if there is a reaction, then the ball mill will form other substances, then the ball mill is meaningless.
- Dry grinding ball mill, due to the design of the ball mill tank, sometimes also forms a dead end, in the dead end of the part of the material that is not ball milling that is dead, this is our daily operation that needs special attention.
Considering the above factors, the choice of dry mill or wet mill needs to be weighed according to the specific circumstances. If the requirements of higher fineness and quality, and the requirements of environmental protection and production efficiency are not high, dry grinding may be more suitable; if the requirements of production efficiency and environmental protection are high, and the fineness requirements are not particularly high, wet grinding is more suitable. Of course, the scope of application and process characteristics of different types of quartz sand ball mills also need to be considered comprehensively.