JXSC Mineral customs manganese ore processing plant & equipment to help you get good solutions for manganese ore.
We are a professional mining equipment manufacturer in China, and have rich design experience for ores solutions. Next we will introduce 2 customized solutions for manganese processing plants.
50 TPH Manganese Processing Plant
Raw Ore Information
- With sticky clay;
- Max feeding size 100mm;
- Mn concentrate size 0-25mm, need be screened out 0-5mm and 5-25mm
- Processing capacity 50 t/h;
- The proportion of big stones and small stones is over 30mm about 50%
- Fe content is about 10%.
Our engineer designed the most suitable and highly efficient flowchart for this project based on the customer’s raw ore information.
50 TPH Manganese Processing Plant Flowchart
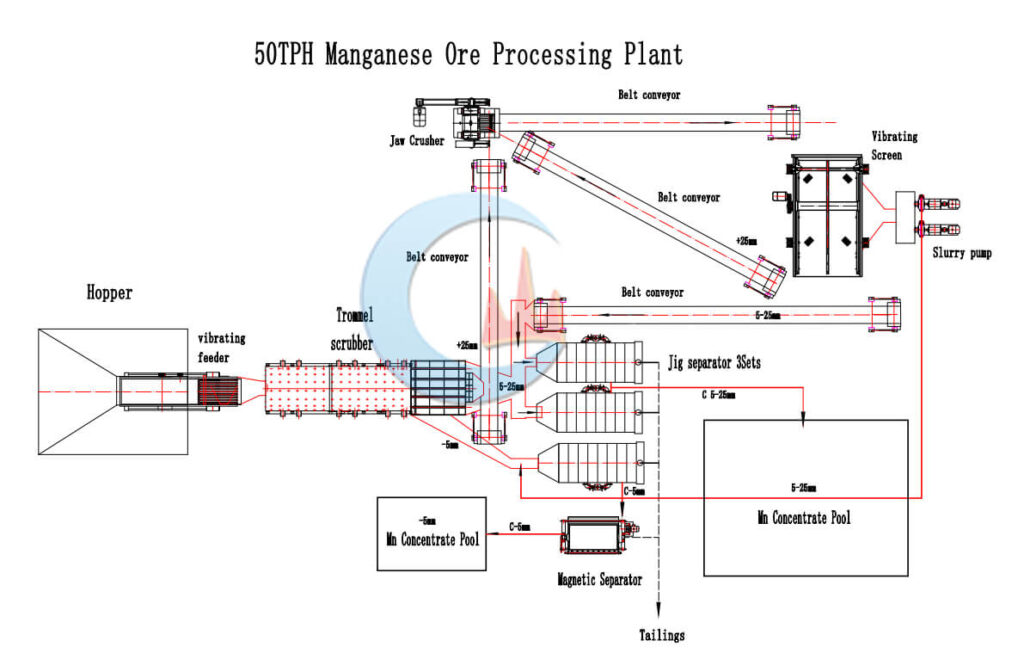
Flowchart explanation
- Vibrating feeder: The loader or excavator feed raw ore into the hopper, through a vibrating feeder to evenly feed the rotary scrubber.
- Rotary scrubber: washing off the clay and screening out 0-5mm,5-25mm, and over 25mm. Our trommel scrubber is configured with the screen at the end, so washed ore go to the screen for sieving out different particle sizes.
- 0-5mm of trommel scrubber go to jig separator for recovery Mn concentrate.
- 5-25mm of trommel scrubber go to another jig separator for recovery of coarse Mn concentrate.
- Over 25mm of trommel scrubber go to jaw crusher via belt conveyor for crushing to a smaller size.
- Jaw crusher: here using a fine jaw crusher, can crush big stones to 0-40mm. The output of the jaw crusher goes to a vibrating screen for sieving out 0-5mm,5-25mm, and over 25mm.
- Over 25mm of vibrating screen are back to fine jaw crusher for further crushing via belt conveyor.
- 5-25mm of vibrating screen go to jig separator via belt conveyor for recovery coarse Mn concentrate.
- 0-5mm of vibrating screen go to another set jig separator via a slurry pump for recovery 0-5mm Mn concentrate.
- All 0-5mm Mn concentrates go to a magnetic separator for removing Fe.
Customer’s Questions
How to increase the Mn grade?
Answer: 1st step washing off clay by trommel scrubber; 2nd step removing Silica sand by jig separator; 3rd step removing Fe by magnetic separator. After these steps, the Mn grade will be increased a lot.
How much the grade can be improved depends on the grade of your raw ore and the proportion of the main mineral components in the raw ore. For example, Mn grade in raw ore is 18%, Silica sand is about 50%, Fe content is about 15%, etc. After you provide these data to me, we can calculate how much Mn grade you will get after the process.
How does the jig recover Mn?
Answer: The jig machine is belong to a gravity mineral separator, it can effectively separate heavy minerals from light minerals. The specific gravity of Mn ore is much heavier than silica sand, so it can easily separate Mn ore from sand and recover the Mn concentrates.
We provided full sets of complete 50tph manganese processing plant installed in Kenya.
Equipment list includes below items
- Vibrating feeder
- Trommel scrubber
- Belt conveyor
- Jaw crusher
- Vibrating screen
- Jig separator
- Magnetic separator
- Slurry pump
- Water pump
- Full sets of auxiliary equipment for installation
100 TPH Manganese Ore Recovery Process Plant
Flowchart
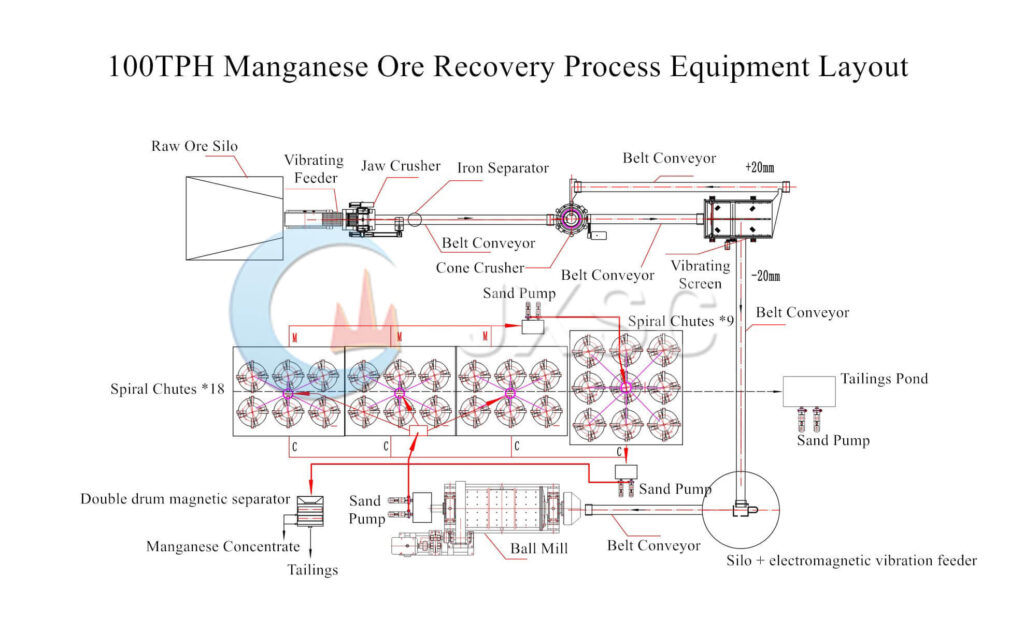
Flowchart Explanation
This setup is for the manganese ore process: raw bin+vibration feeder>jaw crusher>belt conveyor>cone crusher>belt conveyor>vibration screen>belt conveyor>hopper+electromagnetic feeder>belt conveyor>ball mill>slurry pump>spiral chute>slurry pump>double drum magnetic separator.
The raw bin+vibration feeder for feeding materials to the jaw crusher automatically, you only need to load the materials to the raw bin by truck or excavator or else as you want.
The jaw crusher is for crushing the raw ore into small pieces, then to the cone crusher to get the fine sizes.
The vibration screen for separating the size +20mm back to the cone crusher, 0-20mm will to the hopper+electromagnetic feeder, then to the ball mill.
The ball mill is for grinding the 0-20mm materials to 0-1mm, then using the slurry pump to transport the 0-1mm materials to the spiral chute to separate the heavy minerals.
The double drum magnetic separator is for separating the manganese from other heavy minerals, making the manganese concentrate to a higher grade.
The capacity for this washing plant can be customized as per request such as 10tph, 50tph,100tph, etc.,
Notes: The belt conveyor from jaw crusher to cone crusher will need to add the iron remover to make sure the safe and efficient work of the cone crusher.
The spiral chute will normally make two phases, the concentrate from the first phase spiral chute will to the second phase to concentrate again, that will make sure a higher grade and also release the workload of the magnetic separator.
Manganese Ore Recovery Plant Equipment
The equipment used in the manganese ore recovery processing plant
- Vibration feeder
- Jaw crusher
- Belt conveyor
- Cone crusher
- Vibration screen
- Electromagnetic feeder
- Ball mill
- Slurry pump
- Spiral chute
- Double drum magnetic separator
If you need more customized manganese ore processing plant & equipment, please feel free to contact us.