Crushers are mechanical devices or machines that reduce the size of large solid materials into smaller fragments, particles, or powders. They play a crucial role in various industries such as mining, construction, recycling, and manufacturing. Crushers are designed to efficiently break down different materials, including rocks, ores, minerals, concrete, and asphalt.
The primary objective of using crushers is to transform large and bulky materials into smaller sizes that are more manageable or suitable for further processing. By reducing the size of the material, crushers facilitate easier handling, transportation, and storage while enabling the extraction or recovery of valuable components.
What Are The Types of Crushers?
Jaw Crusher
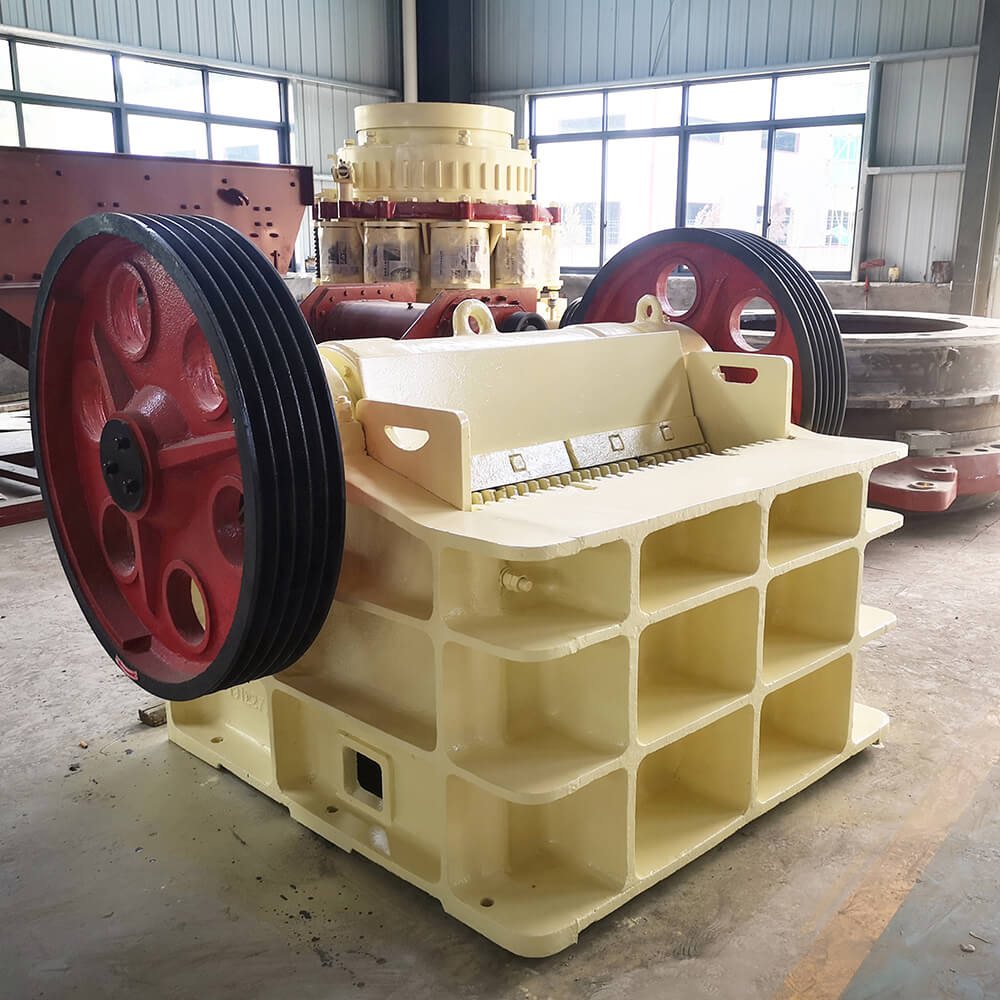
These crushers feature a stationary jaw and a moving jaw that compresses and breaks down materials. Jaw crushers are used for primary crushing and are ideal for materials with high hardness and abrasive properties.
Cone Crusher
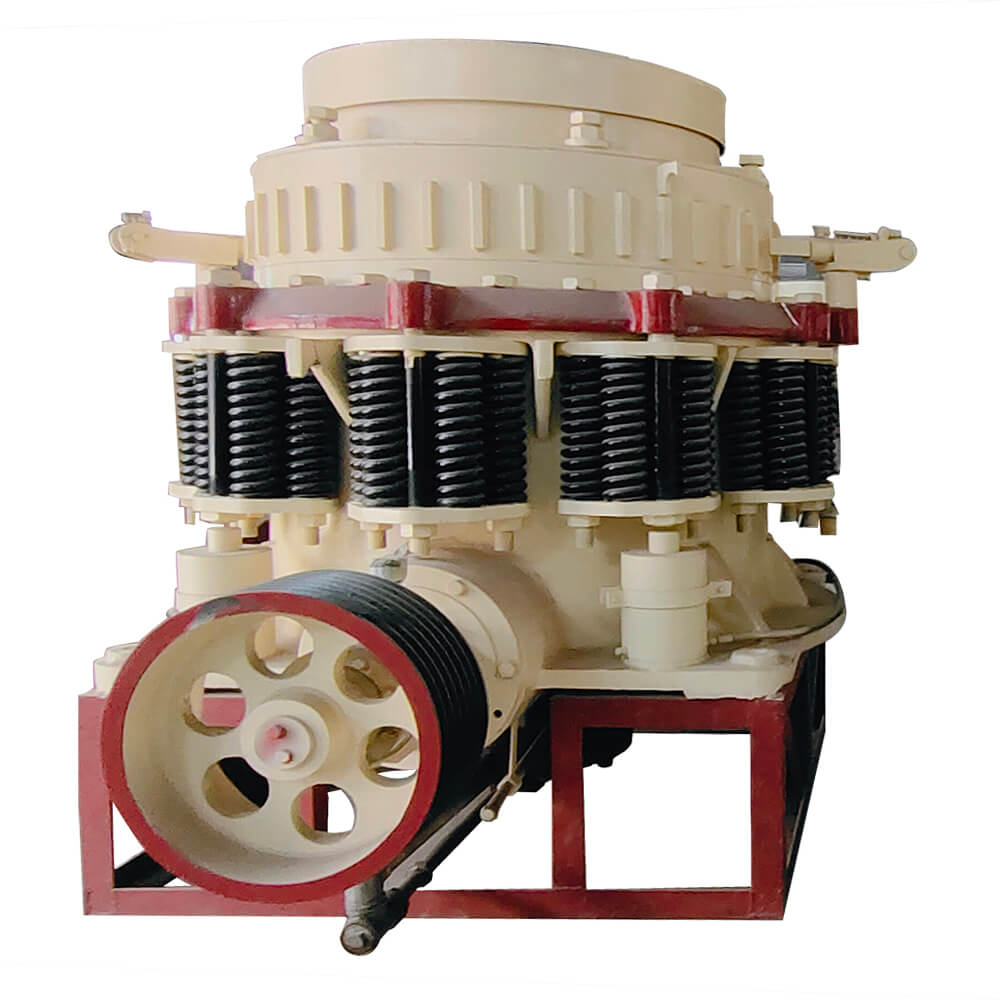
Cone crushers operate by squeezing the material between an eccentrically rotating cone and a stationary concave. They are often used for secondary, tertiary, or quaternary crushing stages and are particularly suitable for crushing hard and abrasive materials.
Impact Crusher
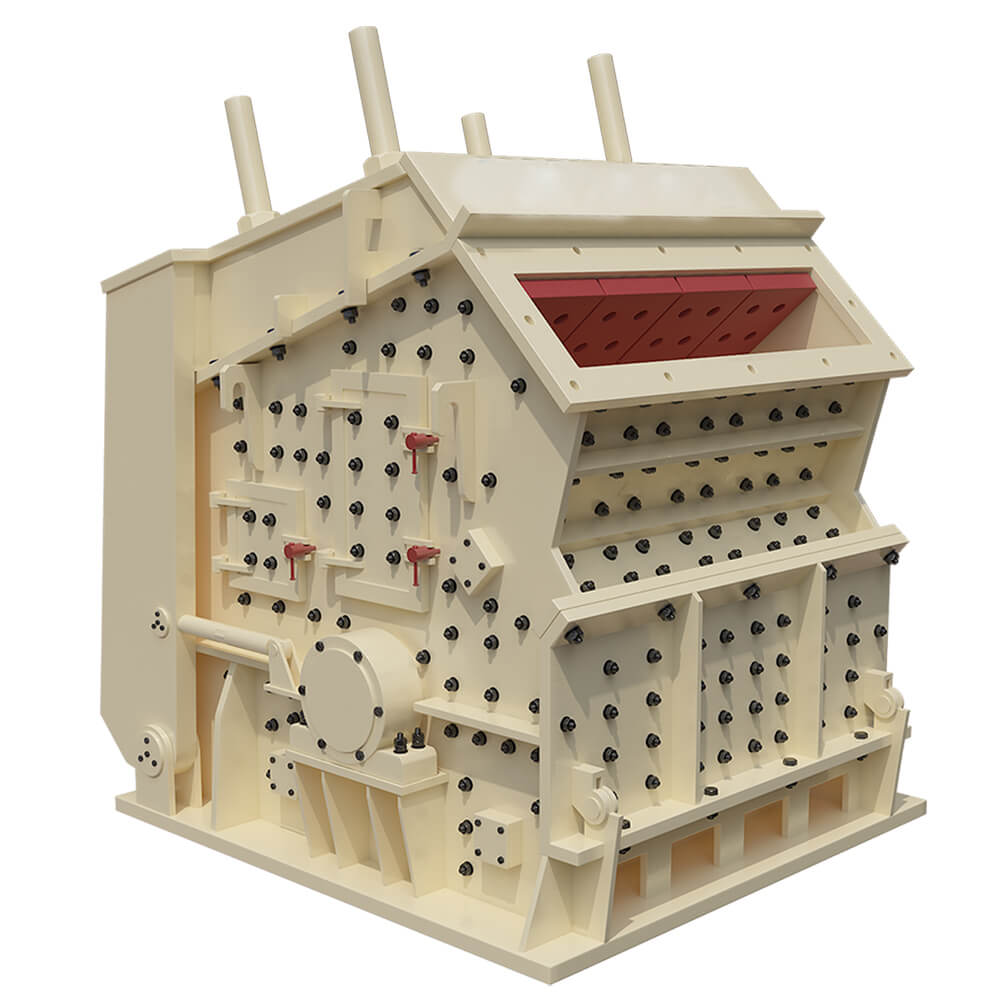
Impact crushers use impact or striking force to crush the material. They utilize hammers or blow bars that strike the material and propel it against a hard surface, breaking it into smaller pieces. Impact crushers are commonly used for both primary and secondary crushing.
Gyratory Crushers
Gyratory crushers comprise a conical-shaped central body that gyrates or rotates eccentrically within a stationary outer shell. Material is fed into the crusher’s top and crushed as it travels down the crushing chamber. Gyratory crushers are often used for primary crushing in large-scale mining operations.
Hammer Mills
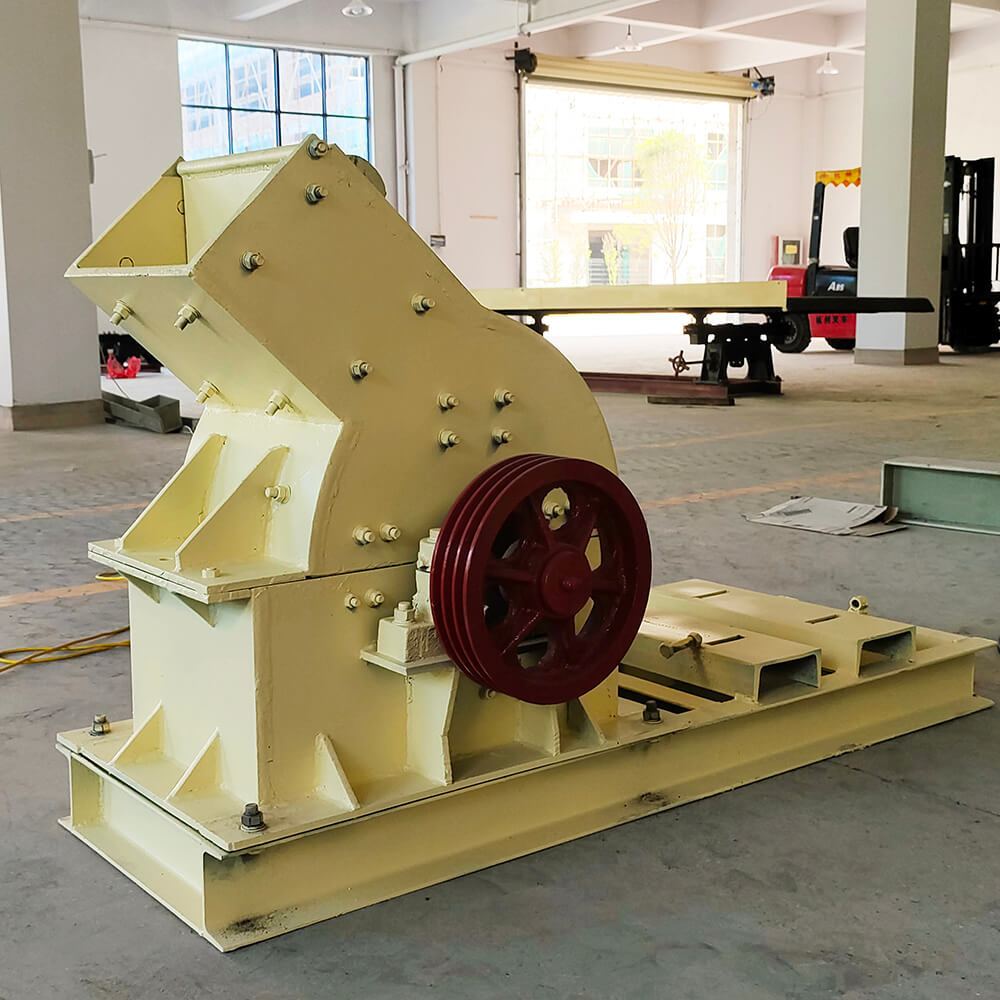
Hammer mills are machines with rotating shafts fitted with fixed or swinging hammers. They are primarily used for crushing brittle materials such as coal, limestone, gypsum, and various industrial minerals.
Roll Crushers
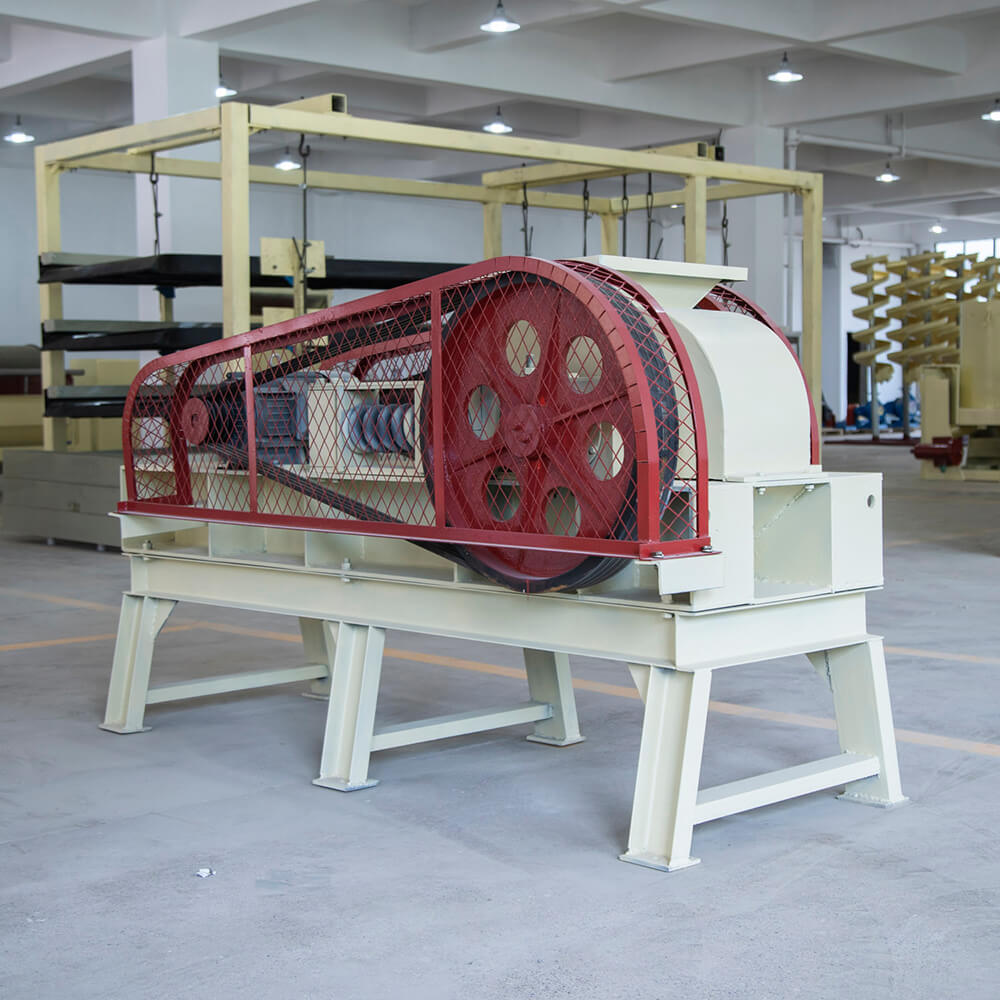
Roll crushers consist of two counter-rotating rollers with the gap between them determining the size of the crushed material. They are used for medium to hard materials and offer a relatively compact design.
Vertical Shaft Impact (VSI) Crushers
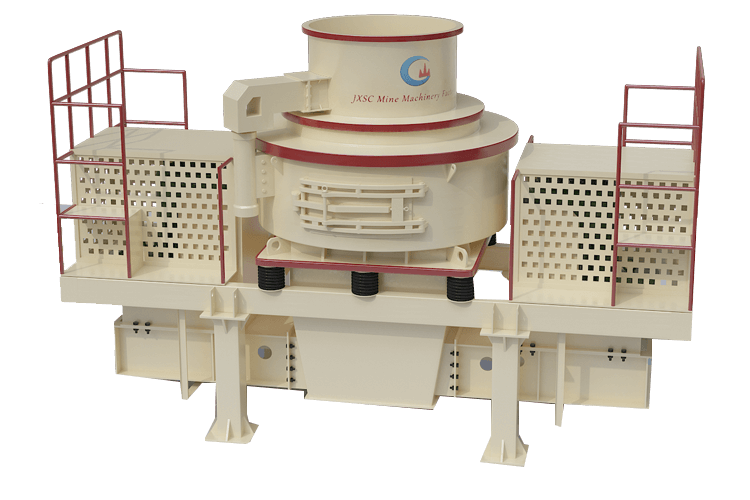
VSI crushers utilize a high-speed rotor with wear-resistant tips or anvils that throw the material against a crushing chamber to break it down. These crushers are mainly used to shape the final product and produce high-quality manufactured sand.
What Are The Standard Crushing Methods of Crushers?
Crushing Broken: This is a common form of crushing in which pressure is applied to an object to cause it to shatter. Place the material between two or more rollers, which either rotate or move to squeeze, flatten and break the material.
Impact Crushing: Impact Crushing achieves shattering by throwing an object onto a hard surface. Materials are impacted and broken. Impact crushing typically uses hammers, hammerheads, or rotating blades.
Shear Fragmentation: Shear Fragmentation breaks the materials by applying a shear force. We usually use this method for fibrous or soft materials. Blades, knives or scissors, etc can achieve shear breaking.
Grinding and crushing: Grinding and crushing breaks materials into fine particles using friction and grinding. We often use grinding and crushing to process hard materials such as ores and mineral sands. We can do it with a rotating millstone or a millstone.
Blast Fragmentation: Blast fragmentation breaks materials by exposing them to explosions or high-pressure gas shocks. This method is often used in the mining and construction industries to deal with huge rocks or concrete.
There are several standard crushing methods of crushers, each with its applicable materials and application scenarios. The crusher usually selects the appropriate crushing method according to the needs to achieve the desired crushing effect.
How to Maintain The Crushers?
1. Bearing maintenance
The bearing part of the crusher is the easiest to break, and it wears a lot during use, so it needs frequent maintenance and frequent refueling to increase the service life of the bearing.
2. Lubrication
Regular attention and timely lubrication of the friction surface can ensure the jaw crusher’s normal operation and prolong the equipment’s service life. The lubricating grease added to the bearing seat is 50-70% of the volume and must be replaced every three months. Clean gasoline or kerosene should be used to carefully clean the raceway of the bearing rollers when changing the oil. When the toggle plate is in contact with the toggle plate pad, lubricating grease must be injected before the crusher starts.
3. Daily life
To ensure that the crusher equipment is in a good technical state, put into operation at any time, reduce the downtime of failures, improve the intact rate and utilization rate of the crusher, reduce the wear and tear of the crusher, and prolong the service life of the crusher, deal with the relationship between use, maintenance, and repair. It is not allowed to use only without maintenance or repair.
What Factors Should be Considered When Selecting a Crusher?
- Choosing a suitable crusher model needs to consider the production demand. Different production needs require other crusher models. For example, for a large-scale quarry or coal mine, choosing a crusher with a larger production capacity is usually necessary to meet production needs. At the same time, it is required for a small-scale construction site to choose a suitable small crusher.
- The crusher model selection also needs to consider the crushed materials. The crushing effect of the crusher is related to the material hardness, humidity, content, and other factors. For example, when crushing limestone or quartz stone with high hardness, choosing a crusher model with a large crushing force and powerful crushing capacity is necessary to ensure efficient crushing.
- The choice of crusher model also needs to consider energy consumption and maintenance costs. Different types of crushers have differences in energy consumption and maintenance. For example, some high-performance crushers may consume more electricity or fuel and require more frequent maintenance, costs that need to be factored into the model selection.
- Considering the degree of automation of the production process, a production line with a higher degree of automation often needs to choose a more intelligent crusher model. These crushers are usually equipped with an automatic control system, which can realize remote control, automatic troubleshooting, remote monitoring, and other functions to improve production efficiency and safety.
JXSC Mineral recommends that when choosing a crusher model, it is necessary to comprehensively consider various factors such as production requirements, crushed materials, energy consumption and maintenance costs, and degree of automation to ensure that the selected model can meet production requirements and have good performance and economic benefits.