The production process of copper ore processing mainly includes crushing, ore grinding, flotation, purification, and drying.
The copper ore that needs to be processed must first go through the crushing process. The vibrating feeder is fed through the silo, and the vibrating feeder is evenly sent to the jaw type for primary crushing, and the large raw ore is broken into small pieces. The coarsely crushed copper ore is screened and sent by the belt. The machine is sent to the cone crusher for intermediate crushing and fine crushing, and the ore is broken into smaller ore particles. The copper ore processed into granules is screened by a vibrating sieve and sent to a ball mill for grinding and crushing. Here also need to use auxiliary equipment – a classifier, which can classify and screen the copper ore and release the copper ore powder that meets the requirements. After the ground copper ore powder is sent to the flotation machine, various rich elements will react with various chemical solvents added to the flotation machine. The flotation machine separates the copper ore from the gangue, the attached metal minerals, the hydrophilicity of copper, and other characteristics. The copper ore extracted by the flotation machine can meet the relevant industrial needs. The copper concentrate powder with high economic value can be obtained after being dried by the dryer.
Crushing
In the crushing process of copper ore processing, the two-stage-closed-circuit crushing-single-stage ball milling process is more common in small copper ore concentrators whose production scale is below 500t/d. Three-stage crushing is currently the most crushing and grinding process used by large and medium-sized copper ore concentrators. The particle size of the crushed products is fine, generally up to <15mm, thus improving the efficiency of copper ore grinding to a certain extent. The so-called new three-stage one closed-circuit crushing-ball milling process refers to the crushing and grinding process composed of a heavy-duty spring cone crusher or hydraulic cone crusher and double-shaft heavy-duty vibrating screen. The crushing particle size of this process can reach about 6mm, which realizes “replacing grinding with crushing” reduces the grinding system’s energy consumption, improves the mill’s processing capacity, and improves the economic benefits of the dressing plant.
Grinding
The combination of copper ore processing and grinding operation equipment is as follows: Small copper ore beneficiation plants mainly use the combination of spiral classifier and mill. Large and medium-sized copper ore concentrators generally use a combination of a mill and a spiral classifier when the grinding particle size is relatively coarse. When the dissociated particle size of the ore is relatively fine and two-stage grinding is required, the equipment combination form of the grinding operation is mill-high weir type spiral classifier/submerged type spiral classifier, or mill-high weir type classifier/hydraulic Combination form of the cyclone. The grinding circuit is optimized by separating the sand return from the spiral classifier and the underflow from the hydrocyclone to obtain a continuous balance of one grinding stage. Due to the large specificity and low hardness of lead-zinc ore, it is easy to be over-grinded. To improve the grinding conditions and increase the recovery rate of copper ore beneficiation, 40% of the existing customers adopt the stage grinding and stage separation process. Using this process can avoid the dissociation of copper ore after one-time grinding. The coarse-grained minerals are caused by over-grinding. In the grinding circuit, an independent flotation cell is used to flotation high-grade materials that are easy to float to reduce the number of materials entering the second stage of grinding, avoid over-grinding of ore, and thus increase the production capacity of the second stage of grinding. Increase the flash flotation operation between the first and second-stage ball mills, take out qualified concentrates accounting for 1/6 of the total concentrate volume in advance, and increase the separation recovery rate.
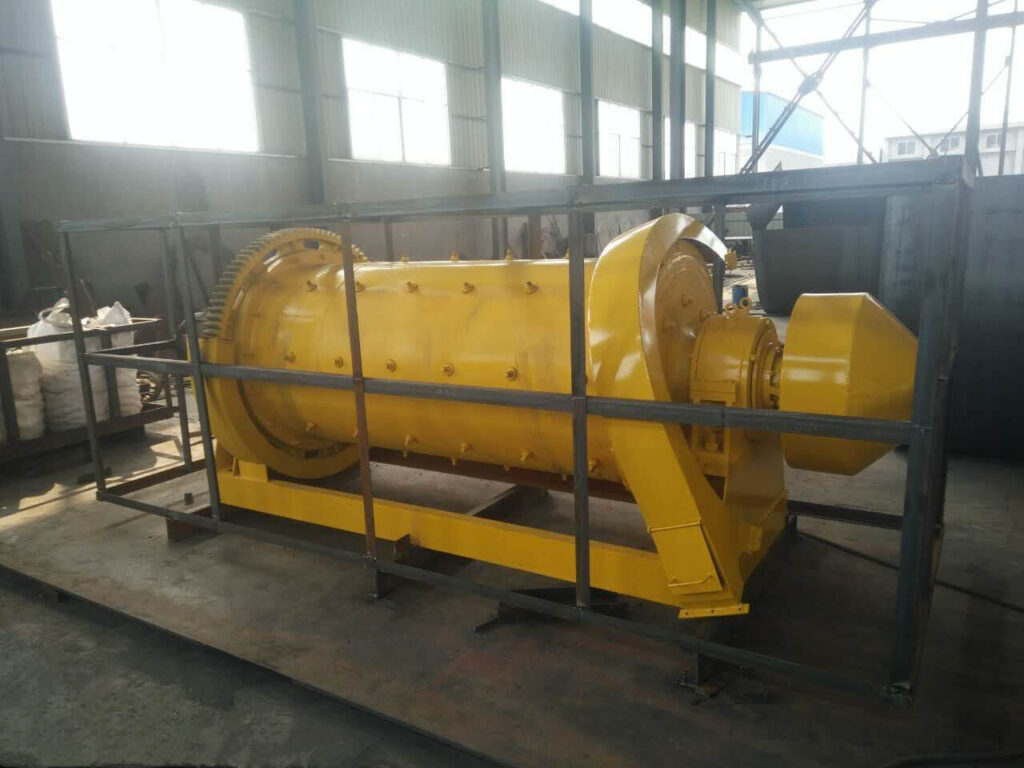
Flotation
In the flotation process of copper ore processing, the collector adsorbed on the surface of the target mineral, which increases the hydrophobicity difference between valuable and gangue minerals. Then the mineral particles with high content of beneficial minerals are adsorbed on the surface of the bubbles, and finally, the air bubbles float up. They are scraped out, completing the flotation process. The flotation functions include dispersing chemicals, stirring, aerating, scraping bubbles, etc., which fully guarantee the smooth progress of flotation. The flotation machine stirs the pulp through the rotation of the impeller, which makes the flotation agent fully dispersed. On the other hand, the coarse minerals in the pulp are kept in suspension under the agitation of the impeller, which avoids the deposition of minerals at the bottom of the flotation tank. The flotation agents dispersed in the pulp are adsorbed on the surface of mineral particles, expanding the hydrophobicity difference between copper ore and gangue minerals.
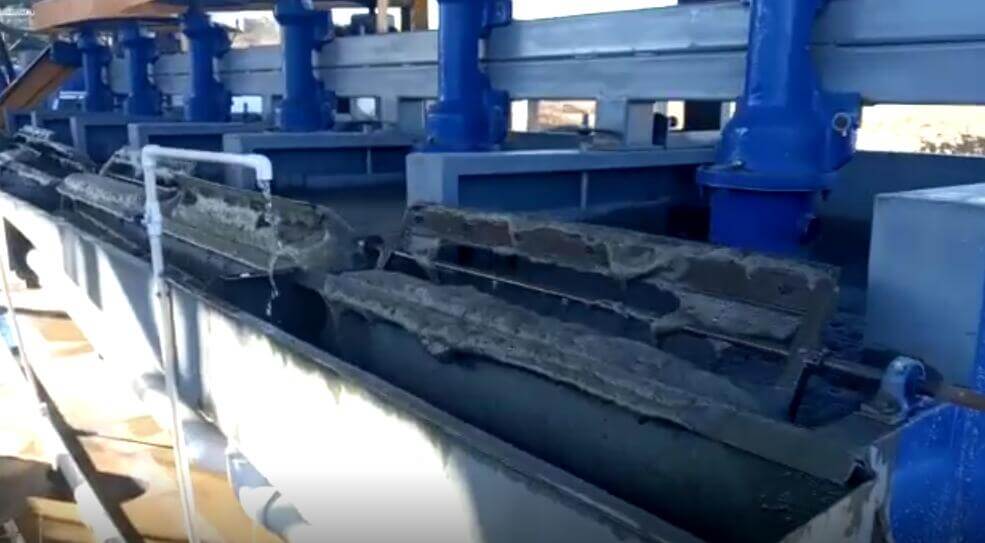
The impeller of the self-suction flotation machine for copper ore processing equipment is thrown out during the rotation process. A negative pressure is formed in the center of the impeller, and the outside air enters the inside of the flotation machine through the suction pipe. The joint between the impeller and the pulp Under the action, air bubbles of small size are formed, which are dispersed in the pulp for flotation. Under the agitation of the impeller, the air bubbles and mineral particles have a certain relative movement speed, and the collision and adsorption are finally completed. Mineral particles with strong hydrophobicity are adsorbed on the surface of the bubbles and rise together with the bubbles and form a flotation foam layer with a certain thickness on the surface of the pulp. Water evaporation, gravity, and other factors break the flotation foam on the liquid surface. The water flow generated by the bursting of the foam has a scouring effect on the foam below, washing away the mineral particles with poor hydrophobicity on the surface of the bubbles and improving the grade of the flotation copper concentrate. Finally, the flotation foam is scraped off by the scraper of the flotation machine to complete the enrichment of copper ore.
Copper ore processing equipment inflatable flotation cell:
- Structural features: no mechanical agitator, no transmission parts;
- Inflatable features: the inflator is inflated, and the structure of the inflator adjusts the size of the bubbles;
- Mixing characteristics of air bubbles and pulp: countercurrent mixing.
- Application: processing rough and sweeping of ores with simple composition, high grade, and easy separation. The flotation column has a simple structure, small footprint, convenient maintenance, easy operation, and power saving.
The characteristics of the inflatable stirring type flotation machine for copper ore processing equipment are:
- The inflation volume is easy to adjust individually;
- The mechanical agitator has little wear;
- The selection index is better;
- Low power consumption.
- The effective inflation volume is large;
- A slurry-up flow is formed inside.
The aeration and agitation of the ore slurry in the mechanical agitation flotation machine for copper ore processing equipment are all realized by the mechanical agitator, which belongs to the external air self-priming flotation machine. Inhale air and self-absorb pulp.