In developing and utilizing copper ore resources, the classification operation of copper ore concentrator is also an important production link of copper ore separation. With the increasing difficulty of copper mining and sorting, the requirements for screening and classification efficiency are getting higher and higher. Therefore, efficient screening and grading equipment is an inevitable choice.
The classification equipment of copper ore concentrators mainly includes spiral classifiers and hydrocyclone. The spiral classifier is primarily used for closed-circuit operation with ore grinding equipment or ore washing, dehydration, desliming, etc., and has a better classification effect on coarser particles. Hydrocyclone, a high-efficiency graded desliming equipment, has been widely used at home and abroad because of its large processing capacity and simple structure.
How to Extract Copper Concentrate From Copper Ore?
Copper ore concentrators use three processes: crushing, grinding, and beneficiation. Only the selection of individual copper ore processing equipment and the beneficiation process will be slightly different.
- In the crushing process, three-stage closed-circuit crushing is adopted, which can satisfactorily complete the work of ore crushing and partial separation, thereby improving the subsequent grinding efficiency;
- During the grinding process, the copper ore can be ground more fully by adopting the two-stage and one-closed grinding process;
- The relatively successful beneficiation process is mainly the mixed flotation process.
The processing equipment and process of the copper ore concentrator are as follows:
The beneficiation and processing of copper ore concentrators are based on flotation. The flotation process of copper monosulfide ore is generally relatively simple and only differs from complex copper sulfide ore in the grinding-flotation structure.
Factors affecting the recovery of copper ore beneficiation mainly include mineral composition, mineral particle size, structure, quantity and storage state of valuable and harmful components, percentage of various minerals, degree of oxidation of minerals, beneficiation process and equipment level, etc.
An Effective Way to Improve the Recovery Rate of Copper Ore Concentrator
The processing technology of copper ore beneficiation plants includes flotation, microbial leaching, segregation, beneficiation, etc. Single sulfide ore is mostly processed by flotation, and copper ore processing equipment adopts the crushing-grinding-classification-flotation-concentration process to select single copper sulfide ore as copper concentrate. However, due to the development and utilization of ore resources, ore properties are becoming more and more complex. Therefore, sulfide ores containing polymetallic can be processed by various methods such as mixed flotation, preferential flotation, mixed preferential flotation, magnetic separation method, flotation method, hydrometallurgy beneficiation method, etc.
Copper Oxide Ore Concentrator
Copper oxide ore concentrators mostly use sodium sulfide pre-sulfurization and then use a single flotation method for selection. However, copper oxide ore, which is challenging to select, is difficult to recover by single flotation. In order to solve the utilization problem of this part of resources, many schemes have been researched. The general trend is to adopt the mineral processing – metallurgy combined process or metallurgical method. The easy-to-select copper oxide ore mainly adopts the flotation method, and the difficult-to-select copper oxide ore mainly adopts the joint process.
The flotation technology of copper oxide ore can be divided into direct flotation and sulfide flotation. Direct flotation refers to the direct flotation of fatty acids and their soaps, advanced xanthate, and other capture agents without pre-sulfurization of minerals, including fatty acids, amines, emulsions, chelating agents, etc. Due to the continuous decline in the mining grade of copper mines and the constant increase in the number of refractory copper mines, it is necessary to continuously improve the beneficiation technology and equipment level of copper mines. The research and application of new flotation methods have created good conditions for the sustainable development of copper ore beneficiation. It is also a development direction that needs further investigation.
Copper Magnetic Separation Process
The magnetic separation process is suitable for the impurities in the copper ore if they are mainly magnetic, and the copper ore tailings magnetic separator is used for copper ore magnetic separation; if the impurities are mainly strong magnetic, the permanent magnetic drum magnetic separator is used to operate. The more times of magnetic separation, the finer the particle size of copper ore, and the better the effect of removing impurities. After the magnetic drum rotates, the electromagnetic vibrating feeder evenly feeds the copper ore to the magnetic field area. With the rotation of the magnetic drum, the magnetic material is adsorbed on the surface of the drum. After the magnetic material is brought to the non-magnetic area along with the magnetic drum, it is unloaded. The non-magnetic and magnetic particles have different throwing trajectories because of their different magnetic forces. Through such a workflow, impurities are removed, and copper is selected.
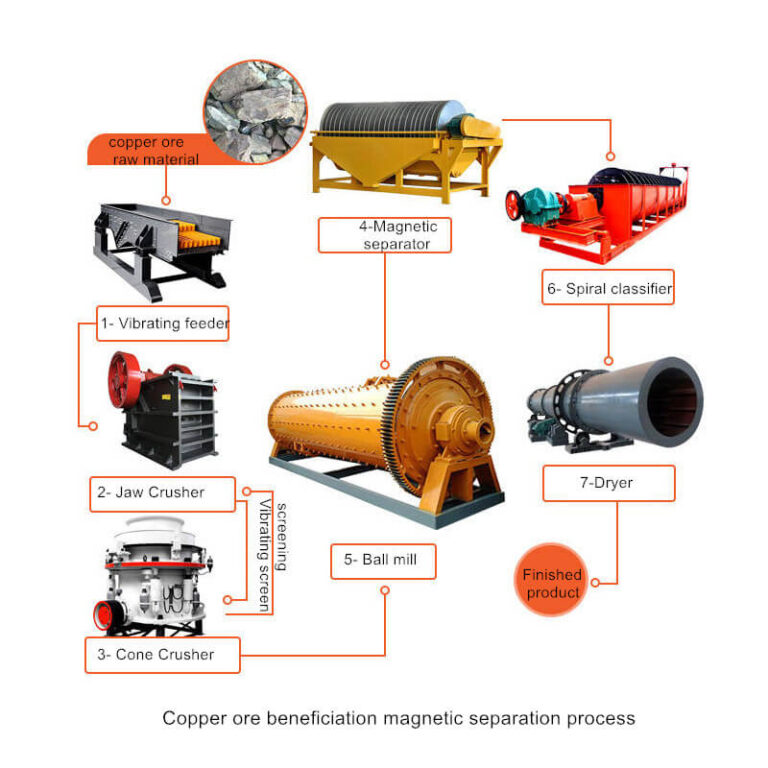
Hydrometallurgical process
The hydrometallurgical process extracts copper or compounds from the purified liquid.
- Transfer the valuable components of copper ore into the solution, that is, leaching;
- The leaching solution is separated from the residue, and at the same time, the metallurgical solvent and copper ions entrained in the residue are washed and recovered;
- The purification and enrichment of the leaching solution, often using ion exchange and solvent extraction technology or other chemical precipitation methods.
In production, electrolytic extraction is commonly used to produce pure metals such as gold, silver, zinc, nickel, and cobalt from the purified solution. Most aluminum, tungsten, molybdenum, vanadium, etc., exist in the aqueous solution in the form of oxyacids and are usually precipitated as oxides first and then reduced to obtain copper.
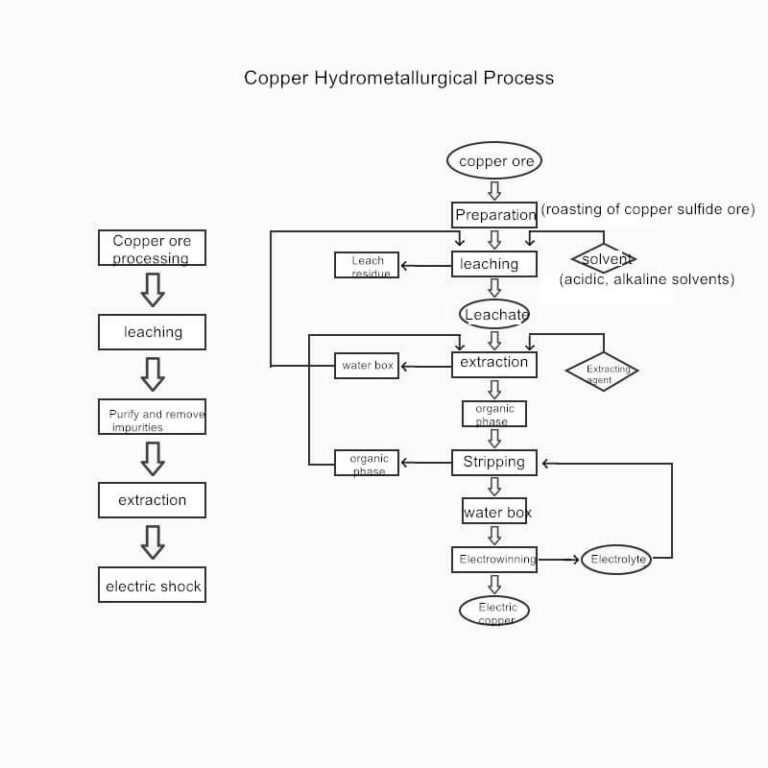
Copper Flotation Process
Crushing and screening → grinding and grading → priority flotation of copper concentrate. Since many copper ores are associated with many other metal substances, copper ore flotation methods are divided into three types.
- Priority flotation
When the copper ore contains two or more valuable minerals and is beneficiated by the flotation method, the valuable minerals are sequentially selected into a single concentrate flotation process. - Hybrid flotation
When the copper ore contains two or more valuable minerals and is beneficiated by flotation, all useful minerals are selected together as a mixed concentrate. Then the various valuable minerals are separated. - Flotation equipment
Due to the strong stirring force of the copper ore flotation machine, the ore particles with relatively large particle sizes and densities can be suspended. At the same time, it can promote the dispersion of refractory chemicals. When the copper ore enters the machine, after layers of processing, it will float to the surface of the pulp together to form a layer of mineralized air bubbles and other mineral particles that are easily wetted by water, which is generally called hydrophilic, do not adhere to the air bubbles. , and stay in the pulp to discharge the mineralized bubbles containing specific minerals to achieve the purpose of ore dressing.
How to choose the copper ore flotation process is selected according to the conditions of the copper ore itself. Different types of copper ores should choose other magnetic separation methods. For example, for more significant copper ores, it is recommended to select the magnetic separation process. The flotation technology of copper ore is constantly improving and the flotation technology of copper ore has also made significant progress, but how to carry out effective flotation processing still needs further effort.