Chalcopyrite is an important copper ore. Since chalcopyrite is often associated with pyrite, improving the separation effect of copper and sulfur is an important technical issue in copper sulfide flotation. Follow we will introduce a copper ore dressing plant that has greatly improved the recovery rate of associated gold mines while increasing the recovery rate of copper beneficiation.
Copper Dressing Plant
Mineral Composition
The minerals in the copper ore concentrator are mainly composed of pyrite, chalcopyrite, copper arsenite, arsenite, tetrahedrite, and sphalerite, the gangue is primarily quartz and sericite, and chalcopyrite is the original ore major copper minerals.
Main Mineral Intercalation Characteristics
1) Chalcopyrite
Chalcopyrite is in the shape of irregular grains, network veins, and veins. Common chalcopyrite is replaced by pyrite and filled in pyrite and gangue. Commonly, chalcopyrite is replaced by tetrahedrite and arsenite tetrahedrite, and the intercalation relationship between the two is very close.
2) Gold minerals
Coarse-grained natural gold is in the shape of irregular dendrites, and fine-grained gold is in the form of round grains, irregular grains, and veinlets. The particles are relatively fine, generally between 0.004 and 0.074mm. The leading carriers of gold minerals are chalcopyrite and tetrahedrite. Intergranular gold is seen in the granular pyrite aggregate particles.
3) Copper minerals containing arsenic
The arsenic-containing copper minerals, arsenite, and chalcopyrite are more closely intercalated, and the phenomenon of arsenic-containing copper minerals filling metasomatic pyrite is widespread.
4) Silver minerals and silver-containing minerals
The particle size is finer, generally 20 μm. The leading carriers of silver are chalcopyrite and tetrahedrite.
5) Pyrite
Pyrite is filled and metasomatized by chalcopyrite and arsenic-containing copper minerals, showing clastic, irregular granular, round shapes, and some network-veined and veinlet-shaped pyrite and arsenic-containing copper minerals are filled in the fragmentation. In the fissures of pyrite, it isn’t easy to dissociate the monomers due to the fine particle size of the embedding.
6) Gangue minerals
The aggregate particles of gangue minerals in the raw ore are relatively coarse and easy to dissociate.
Introduction of Beneficiation Process
The processing capacity of the copper system of the plant is 6500t/d. Because of the fine particle size and tight combination of copper and sulfur intercalation in this mineral ore, the associated gold is distributed between chalcopyrite and pyrite in ultra-fine particle size, while valuable minerals and gangue intercalation. The particle size of the cloth is relatively coarse, and the technological process of “copper-sulfur mixed floating-mixed concentrate, then grinding and separation” is generally adopted for this kind of ore.
The first stage of grinding adopts the SABC process. The raw ore is coarsely crushed to a particle size of ≦350mm in the mining field and then fed into a Φ7000mm×3500mm semi-autonomous mill. Return to the semi-autogenous mill after crushing, send the under-screen part and the ball mill discharge into the Φ660mm cyclone group for classification, and the cyclone settling sand enters a Φ4800mm×7000mm overflow ball mill for grinding. The overflow of the concentrator enters the first-stage copper-sulfur mixed flotation operation. The coarse concentrate of the copper-sulfur mixed flotation operation enters the Φ350mm cyclone group for classification. The sand enters a VTM-800-WB vertical mill for the second-stage grinding, ≤45μm content of 85% of the cyclone overflow into the second-stage copper-sulfur separation operation, the output of copper concentrate and sulfur concentrate. The flow chart of copper system beneficiation in this plant is as Figure 1.
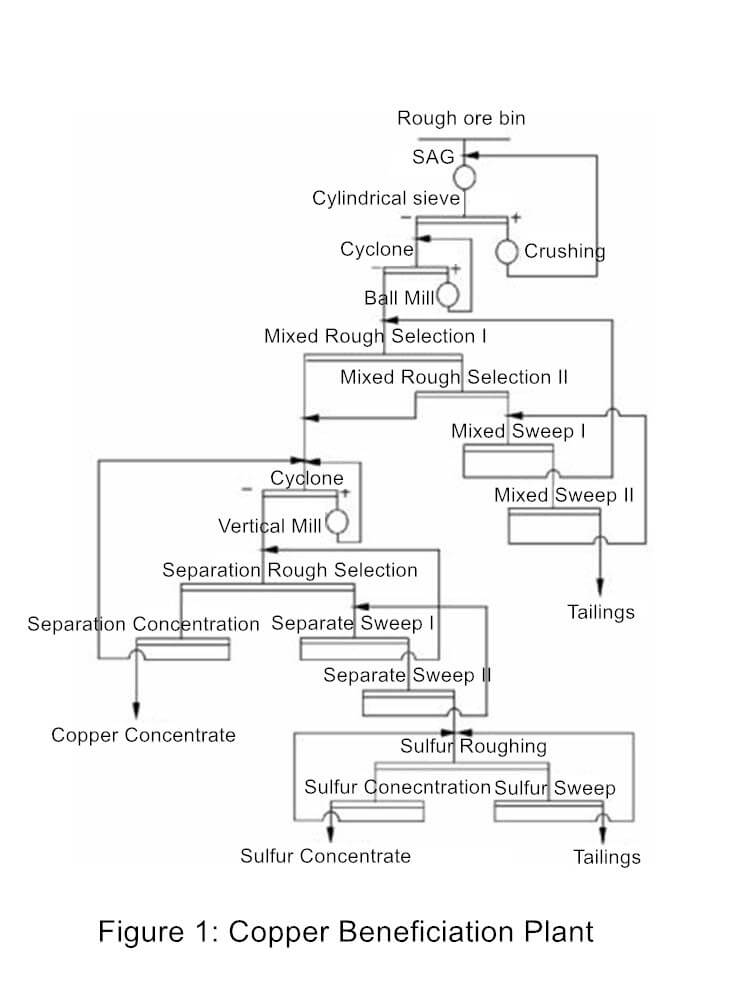
Improvement Measures
Grinding Fineness Improvement
Appropriate grinding fineness is crucial for sufficient dissociation of valuable minerals in the ore and cost reduction. Whether the grinding class is suitable directly affects the quality of the sorting index. A better-grinding fineness ensures the dissociation of the target mineral monomers and prevents over-grinding. In order to understand the influence of grinding fineness on the recovery rate of copper in the first-stage copper-sulfur mixed separation operation, the raw ore and tailings of the first-stage flotation operation were screened and tested. The results of the testing machine show the tailings loss rate of ≥178μm and ≤38μm is relatively high. If it can reduce the content of the above two particle sizes, it will increase the recovery rate of copper in the first stage of the mixing operation.
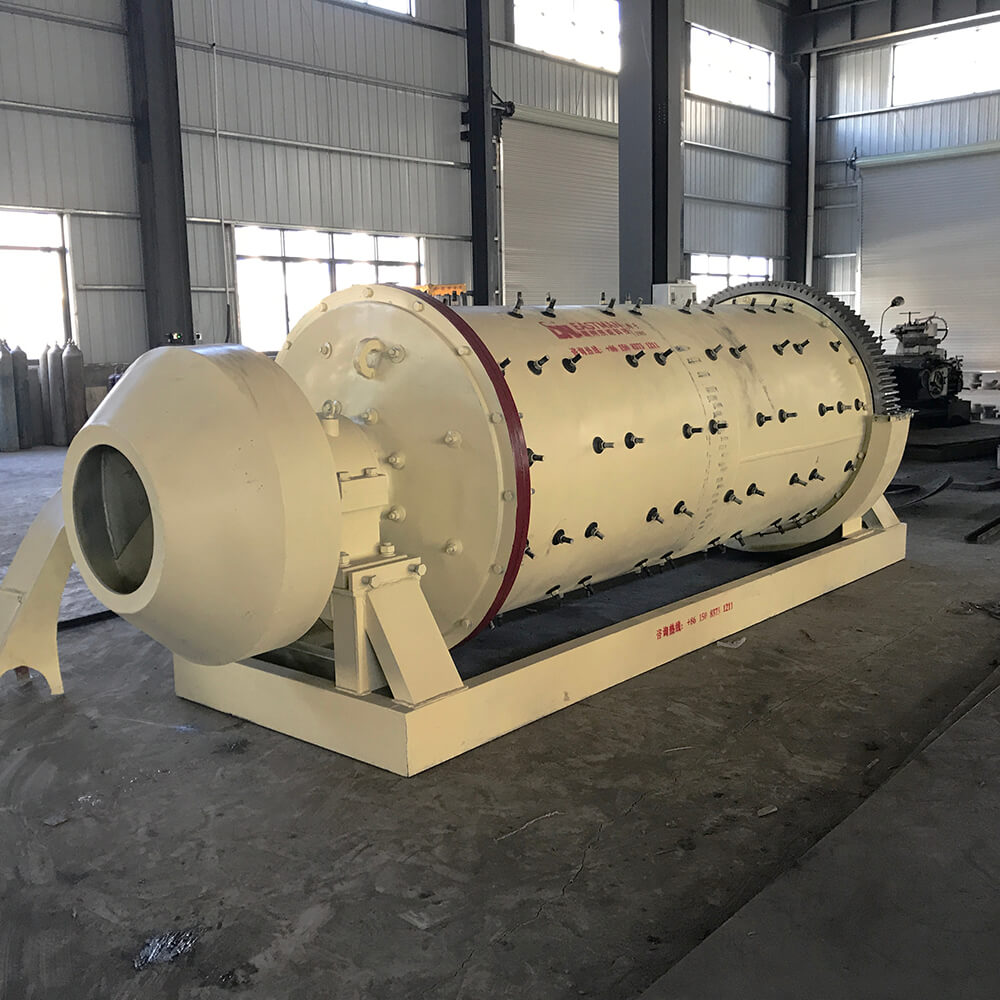
The effect of the grinding operation is closely related to the ball mill grinding effect and the classification efficiency of the classification operation. The plant is as follows: the steel balls added to the semi-autogenous grinding were Φ125mm forged balls, and the mills were Φ80mm steel balls. The filling rate is about 8.5%, the ball milling ball filling rate is about 30%, the diameter of the grit nozzle of the first-stage cyclone is 120-135mm, the operating power of semi-autogenous grinding is mostly 1500kW/h, and the installation of semi-autogenous grinding is 2500kW/h 60% of h. In order to balance the grinding load and optimize the particle size distribution of grinding products, the factory reduced the diameter of semi-autogenous grinding supplementary steel balls from Φ125mm to Φ100mm. The ball mill supplementary balls changed from Φ80mm to Φ70mm: 50mm2 Steel balls with different diameters are added at a ratio of 2:1, and the diameter of the grit chamber of the cyclone is strictly controlled within the range of 120-130mm.
By adjusting the diameter of the additional ball and the diameter of the settling nozzle in the grinding operation, the content of ≤74μm in the first-stage grinding process increased by 2.61%, while the content of the difficult-to-float particle size ≥178μm and ≤38μm decreased by 2.05%, is conducive to improving a copper recovery rate.
Lime Dosage Improvement
In industry, the commonly used inhibitor of pyrite is lime because of its vast source and low price. However, the excessive lime dosage will also inhibit copper sulfide minerals and gold. It carries a copper separation roughing experiment in the laboratory to understand the influence of lime on copper recovery rate and concentrate grade. It selects Z200 as a collector in copper-sulfur separation operation because (isopropyl) thiamine ester——Z200 has good selectivity to chalcopyrite flotation, and its ability to collect pyrite is worse than that of xanthate. The amount of Z200 is 125g/t, and the amount of lime is variable.
The test shows that when the amount of lime used in the second-stage roughing increases, the operation’s recovery rate decreases, and the concentrate grade gradually increases. In order to create conditions for the beneficiation operation to improve the concentrate grade, the amount of lime for separation and roughing is determined to be 2.0kg/t.
Improvement of the liquid level of the flotation machine
We conducted on-site debugging on the relationship between the liquid level of the flotation machine and the grade of concentrate to improve the copper concentrate grade. The rest of the work on-site remains unchanged, and the fluid level is adjusted every 2 hours. The concentrate and tailings grades are based on the on-site fluorescence detection data.
From the adjustment results of the liquid level of the flotation machine, it seems that with the continuous increase of the thickness of the foam layer, the quality of the copper concentrate is continuously improved. Still, the grade of the flotation tailings hardly changes much, but when the thickness of the foam layer reaches 1350mm, the separation tailing Mine starts to get high. Through the adjustment test of the flotation machine, the adjustment range of the liquid level of the flotation machine is specified between 600 and 300mm, and the operator can make appropriate adjustments according to the grade of the raw ore.
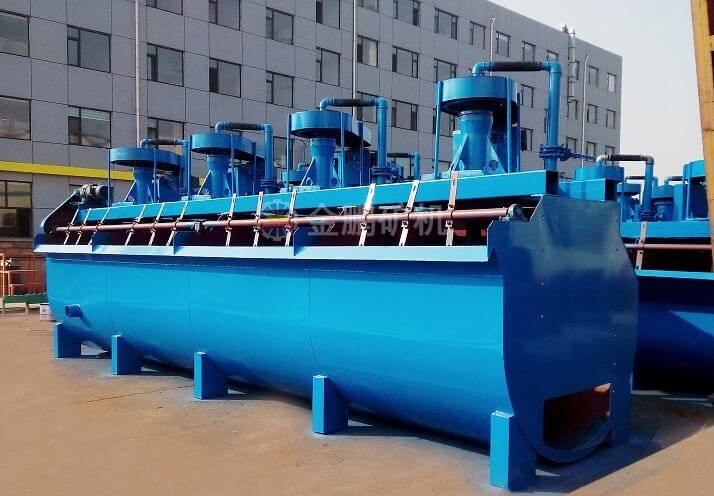
Through a series of improvements, the beneficiation index of the copper system has been improved. At the same time, due to the increase in the copper recovery rate, the gold recovery rate has also increased from 42% before improvement to 46% after improvement.
Improvement Effect
- Through the use of MA-1 and MOS combined collector instead of xanthate in the sorting process and the improvement of the addition system of semi-autogenous and ball-milled steel balls, the recovery rate of copper in the first stage of selection has been significantly improved.
- The vertical mill is used instead of the traditional ball mill for the secondary grinding, effectively improving the grinding fineness and creating conditions for the flotation of copper and gold minerals.
- By reducing the amount of lime and improving the liquid level adjustment parameters of the flotation column, the separation effect of copper and sulfur in the second stage is improved, and the recovery rate of copper and gold is improved.