A cone crusher is a kind of medium and fine crushing equipment, which is mainly used to produce stone size, and its discharge particle size is less than 5 cm. It can process 0-5mm, 5-10mm, 10-20mm, and 20-40mm four kinds of stones.
Hard rock is a material with a Mohs hardness greater than 5, represented by granite. Generally speaking, it often uses the jaw crusher, impact crusher, and cone crusher to crush this hard rock. But through the comparative analysis of crushing efficiency, finished particle shape, and wear rate, the cone crusher is more suitable for crushing hard rock.
Reasons for Choosing Cone Crusher For Hard Rock Crushing
- Because the hard rock is hard, it will cause great wear and tear to the equipment when broken.
The counterattack type adopts the principle of impact crushing. The high-speed moving plate hammer is used to impact the material to break, and the plate hammer bears the brunt, so it will accelerate the replacement frequency and delay production time.
A cone crusher is one of the most common medium and fine crushing equipment in mines.Its working principle is lamination crushing, which uses couplings, transmission shafts, etc., to drive the crushing wall to swing slowly. And the force of impact and extrusion on the material results in crushing. Cone crushers are suitable for crushing ores and rocks of medium and above hardness, with high productivity and easy maintenance. They are widely used and trendy in the market. The cone crusher is broken in layers, significantly reducing wear and tear. So the cone crusher is more suitable for crushing hard rock than the impact crusher.
2. The particle size of the finished rock is uniform, and the crushing efficiency is high.
Although the particle shape of the finished hard rock after cone crushing is not necessarily better than that of the impact crusher, it has fewer needle-like substances, and the particle size of the finished stone is relatively uniform. Furthermore, the crushing efficiency of this machine is high. For enterprise users under general production requirements, it is pretty good to choose cone crushing.
3. High safety performance.
The cone crusher adopts a spring hydraulic safety device. When unbreakable foreign objects or the equipment covering the crushing cavity is overloaded, it can automatically enlarge the outlet to discharge foreign objects to ensure its safety. The other ordinary crushers do not have this function, so it is more suitable for hard rock crushing than other equipment.
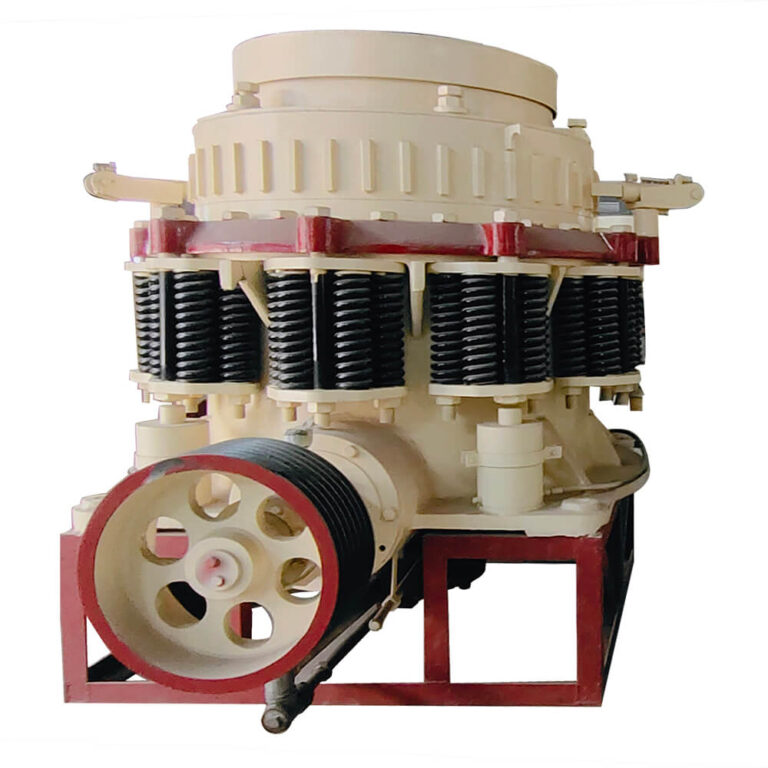
Generally, configuring the hard rock crusher plant will select some auxiliary crushing equipment to complete the coarse crushing and shaping of hard rock materials. Such as the jaw crusher, impact crusher, and sand-making machine. The specific crushing process is as follows.
First, the hard rock is crushed by the jaw crusher, then conveyed by the conveyor belt to the cone crusher for processing and crushing, and then enters the impact crusher (sand-making machine) for shaping. If the requirements for finished products are high, you can also choose a sand washer to clean and screen the finished sand and gravel.
What Factors Affect The Cone Crusher’s Capacity?
When many people use cone crushers for production, they will encounter the situation that the production capacity is not up to standard. The output of cone crushers is affected by many factors. The following will introduce three internal factors that affect the performance of cone crushers.
- Length of crushing parallel zone
The crushing parallel zone is the guaranteed zone for the uniform particle size of the cone crusher. The parallel zone’s starting point is the crushing cavity’s clogging point. The length of the parallel zone determines the position of the clogging point, which affects the thickness of the material layer. The length of the parallel zone will affect not only the cone crusher’s particle size but also the cone crusher’s discharge capacity. The reduction of the length of the parallel zone is conducive to the discharge of ore, but the particle size of the crushed ore is not easy to guarantee; the length of the parallel zone increases and the discharge capacity is reduced, But it is beneficial to control the granularity. The size of the meshing angle
The cavity shape of the cone crusher is the working space formed by the crushing wall (moving cone) and the rolling mortar wall (fixed cone), and the meshing angle is the angle between the rolling mortar wall and the crushing wall of the cone crusher. The size of the angle will affect the cavity capacity of the crushing cavity. The meshing angle is generally 22° or 23°, and the maximum is 27°. Theoretically, suppose the cone crusher’s meshing angle is too large, and the crushing cavity is large. In that case, the ore will easily slip into the crushing cavity and reduce the production capacity. If the meshing angle is too small, the crushing cavity will be too small. The amount of ore that the hole can hold will also be relatively reduced, thus affecting the capacity of the cone crusher.
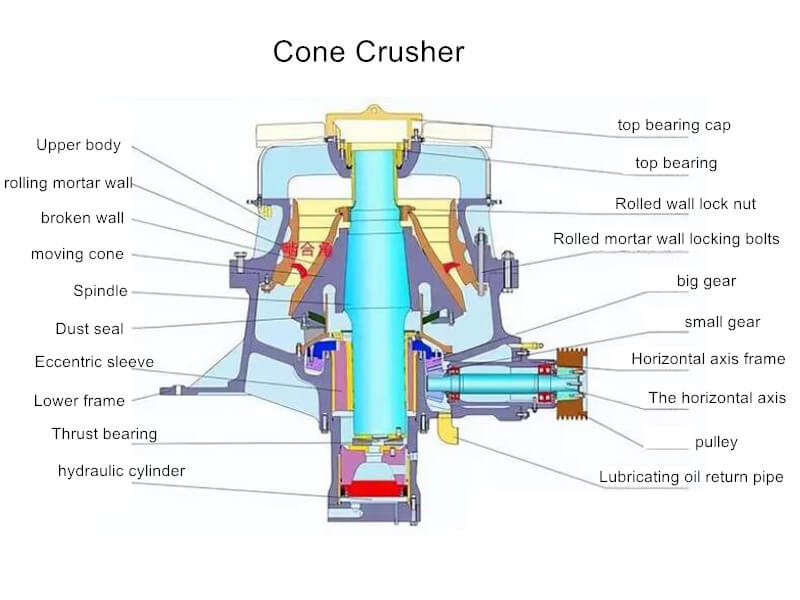
- The rotation speed of the moving cone
The material is crushed by the moving cone’s and static cone’s extrusion and impact, and the crushed ore is mainly discharged along the cone’s slope by its gravity and vibration. When the rotating speed of the moving cone is too slow, the discharge speed of the material will also decrease, resulting in lower output and worse particle size. The material can’t discharge normally, resulting in blockage, which makes the cone crusher overloaded and unable to produce.
In addition to the three external factors that affect the performance of the cone crusher, other internal and external factors will affect the production capacity of the cone crusher. To ensure the cone crusher’s capacity, first, choose a high-quality cone crusher supplier. If you want a high-quality cone crusher, you can select jxsc mineral.