The mineral processing equipment commonly used in mineral processing plants includes crushing, grinding, screening, magnetic separation, flotation, etc. Following we will analyze and discuss the wearing parts of screening, magnetic separation and flotation equipment, and the leading causes of wear.
Screening Equipment
Screening equipment is the equipment used for material classification. Many types of screening equipment are commonly used in mineral processing plants, including grading screens, high-frequency screens, and linear screens. The wearing parts of the screening equipment are mainly screens, fasteners, and bolts. The main reasons for the wear of these wearing parts are the nature of ore, excessive ore feeding, and the impact of materials.
- Ore properties.For screening equipment, the most common problem affecting screening efficiency is sieve clogging, and the degree of sieve clogging is closely related to the shape and water content of the feed material. If the water content of the ore is too high, it will cause the ore to be relatively sticky and not easy to separate, resulting in blockage of the sieve holes; the ore particles are long strips, which are relatively difficult to sieve and will also cause blockage of the sieve holes.
- The ore supply needs to be more significant. In production, it is usually required to feed the ore as evenly and stably as possible to avoid overload operation. Excessive ore feeding will reduce the screening efficiency and cause ore accumulation or crushing, which will cause screen damage, coupling fracture, sc
- The sreening box cracking, and other faults.
- The impact of the material.For the screening equipment of the crushing system, the maximum force it bears during operation is the impact force of the feeding material. The strong impact not only causes the screen to break but also causes damage to the body and bolts of the equipment to a certain extent.
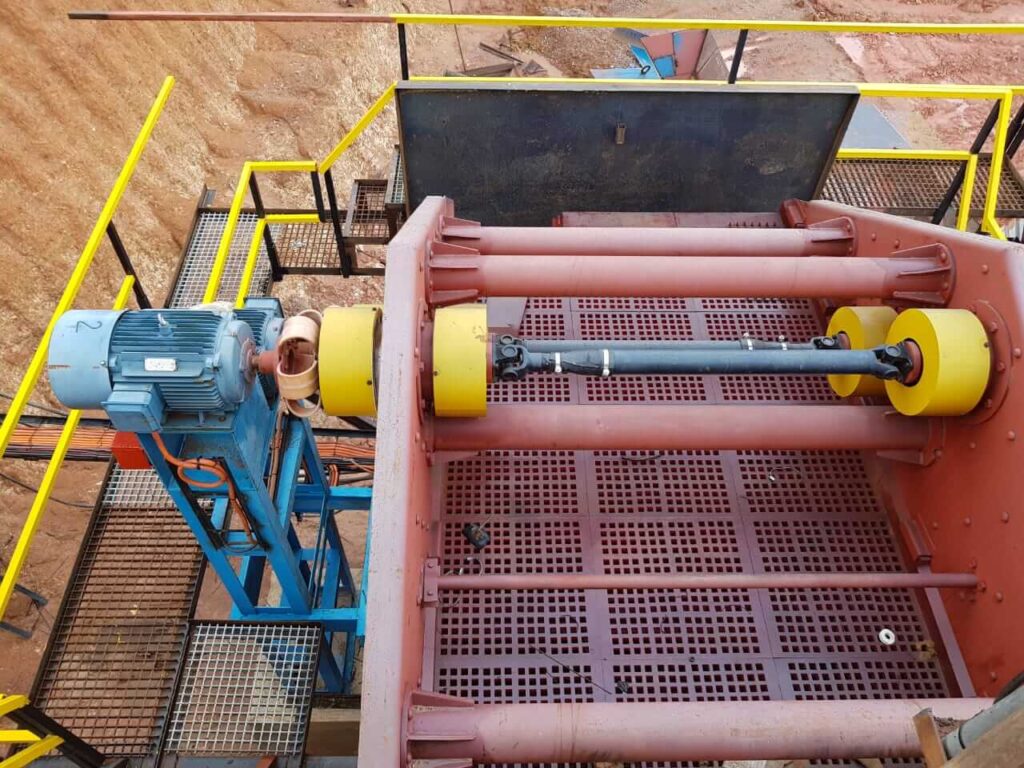
Magnetic Separation Equipment
According to the strength of the magnetic field, the magnetic separator can be divided into a weak magnetic field magnetic separator, a medium magnetic field magnetic separator, and a strong magnetic field magnetic separator. At present, the wet drum magnetic separator is the most widely used, and the wearing parts include drum skin, magnetic block, tank bottom, transmission gear, and so on. The main reasons for failures are large-scale debris entering the magnetic separator, magnetic block falling off, magnetic block performance degradation, and poor lubrication effect.
- Large-scale debris enters the magnetic separator.If a large volume of debris enters the magnetic separator, it will scratch the cylinder skin if it is light, and it will jam the cylinder if it is serious, causing the equipment to stop; in addition, it may also grind holes in the tank body, resulting in ore leakage in the tank body.
- The magnetic block falls off. When the magnetic block in the magnetic separator drum falls off seriously, the drum skin will be scratched, and it needs to be stopped for maintenance immediately.
- The performance of the magnetic block is degraded. The service life of the magnetic separator is too long, the performance of the magnetic block is degraded, and the magnetic field strength is reduced, thus affecting the separation effect.
- The lubrication effect could be better. Poor lubrication will lead to problems such as transmission gear wear.
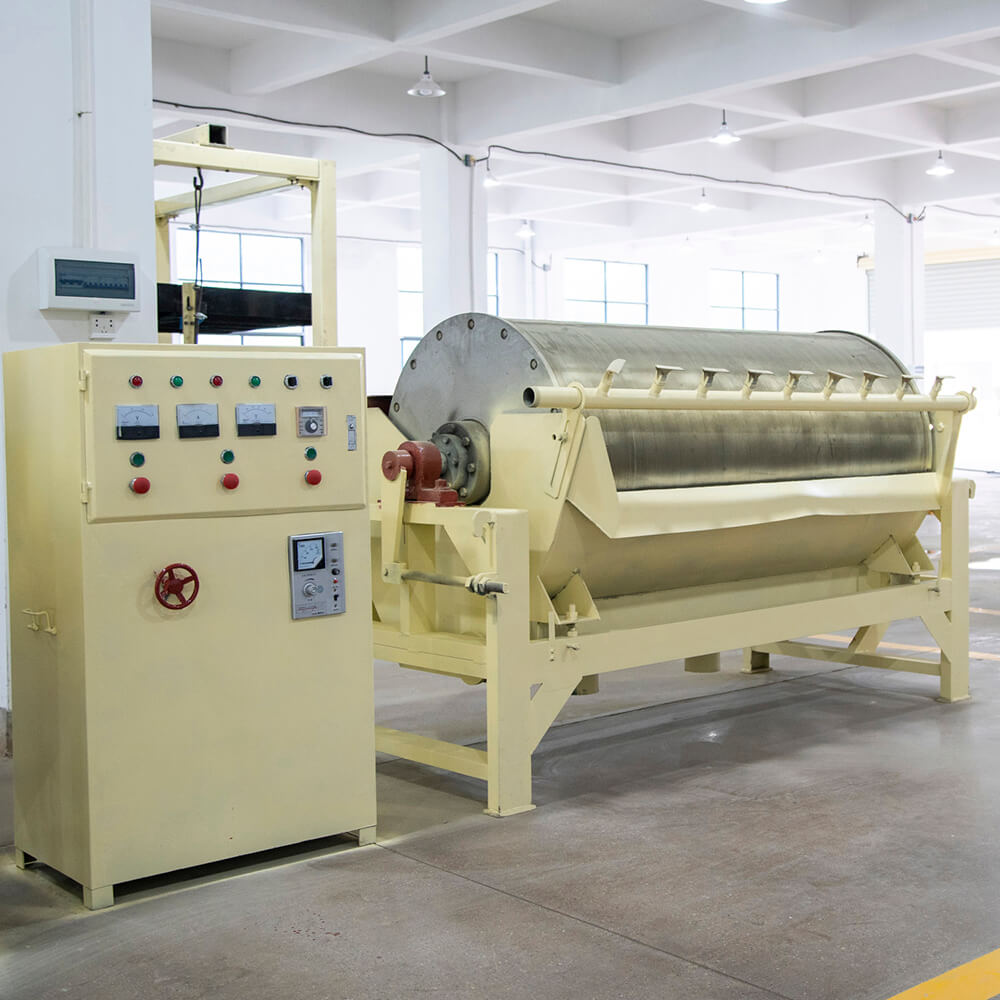
Flotation Equipment
The wearing parts of the flotation machine mainly include the stirring device, scraper device, tank body, gate device, and so on.
- Stirring device.The stirring device mainly refers to the impeller, whose function is to make the agent fully contact with the mineral particles and plays a critical role in the flotation process. When the stirring device fails seriously, it will cause the flotation machine to press ore, affecting the regular operation of the flotation machine. The common problems of the stirring device are mainly loose nuts, poor lubrication, a loose connection of the stirring part, etc.
- Scraper device.The scraper of the flotation machine is installed on both sides above the tank of the flotation machine. The scraper shaft is ultra-slender, and the machining accuracy is difficult to control, so there will be problems of poor precision; in addition, the scraper device is used during transportation, During the installation process, due to problems such as hoisting and transportation deformation, the rotation of the scraper shaft is not flexible, and the scraper shaft is broken.
- Tank body. The common problem of the tank body is water seepage or water leakage, which hardly affects the beneficiation effect if it is not serious. Still, it has a great impact on the surrounding environment. The leading causes of water seepage and leakage in the tank are weld defects, tank deformation, and loose flange connection.
- Gate device. The ram device is a mechanism to control the liquid level. It is installed at the tail of the flotation machine. Frequent adjustment of the flotation machine ram will cause damage to the hand wheel. In addition, the more common ram failure is poor lifting, which is generally caused by poor lubrication of the screw. , screw corrosion, jamming, and other problems.
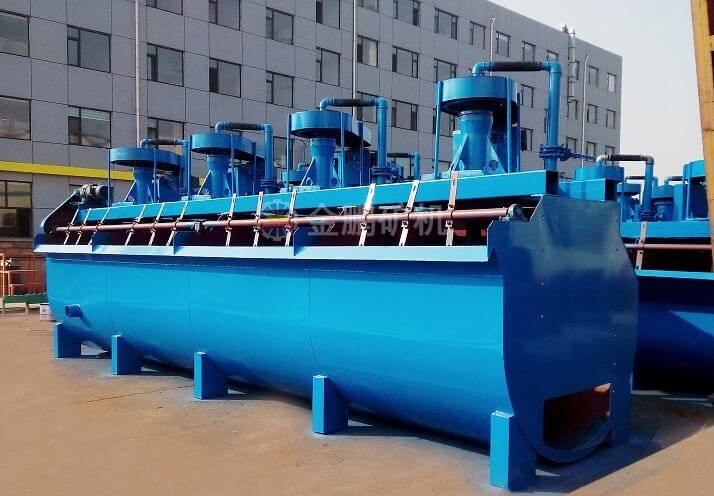
In mining enterprises’ daily production and operation, mineral processing equipment occupies a significant position. It plays an irreplaceable role in the entire mineral processing process, but equipment operation will inevitably be affected by many factors, resulting in equipment failure. It requires an in-depth analysis of the causes of equipment failures, strengthening daily maintenance and repairs, improving management systems, introducing more advanced mineral processing technology and technical equipment, improving production efficiency, reducing the incidence of equipment failures, and boosting the sustainable development of the mining industry.