Belt conveyors are widely used in all walks of life due to their advantages of strong transportation capacity, high tensile strength, soft belt body, long life, and good economy. However, due to the influence of many factors, belt breakage in belt conveyors has become a common accident. Once a belt break occurs, it will not only seriously affect production efficiency. Still, it may also cause safety accidents, so it is crucial to understand the causes of accidents and preventive measures.
Belt Conveyor Belt Breakage Cause Analysis
There are many reasons for the belt conveyor to break. The following are some common reasons.
Belt Conveyor Quality
The belt conveyor tape quality is not up to standard
As an important part of the belt conveyor, the role of the tape is to carry the minerals and transport them to the designated location. However, if the quality of the tape used by the company is not up to standard, coupled with the service life is too long, overload operation or routine maintenance is not in place, etc., This causes belt breakage accidents due to the material being too lumpy and the conveyor getting stuck.
The quality of the belt conveyor joint is poor
Belt conveyor joints are divided into mechanical joints and vulcanized joints. The former is not as good as the latter and is rarely used now.
The joint is the connection point between the two belt conveyor belts. If its quality is not good, it will likely cause a belt breakage accident. The joint will often break in the following four situations:
- During the use of vulcanized joints, dust often covers the steel wire and rubber material, causing the latter to rust or open and causing the joint to break.
- During the local vulcanization process, if the steel wire core tape joint is in a tensioned state, heating at this time will cause small twitching in the steel wire rope and rubber layer, thereby increasing the possibility of joint breakage.
- If the materials used by the belt conveyor joint manufacturer do not meet the standards, they will easily be worn, corroded, and become brittle, which will easily lead to breakage under strong force.
- The vulcanization process standards used in the production of joints are not up to standard or strictly implemented. If the quality of the joints produced is not up to standard, breakage accidents will occur.
Belt Conveyor Installation
- Improper Installation: Incorrect conveyor belt installation or components can cause misalignment, tension issues, and other problems that may contribute to breakage.
- Belt Misalignment: If the conveyor belt is not properly aligned on the rollers or pulleys, it can cause uneven stress, leading to breakage.
- Belt Tension Issues: Incorrect belt tensioning, either too tight or loose, can affect its performance and contribute to breakage.
- Tensile Strength: The rated tensile strength of the belt exceeds the standard during transportation.
Belt Conveyor Use
- Overloading: The transportation load suddenly increases due to the involvement of other things during transportation, such as large pieces of gangue or other huge objects suddenly mixed in the transported materials. Exceeding the designed capacity of the conveyor can lead to excessive stress on the belt, resulting in breakage. It’s essential to operate the conveyor within its specified load limits.
- Material Contamination: Abrasive or sharp materials transported on the conveyor can cause wear and tear on the belt, leading to eventual breakage.
- Material Jams: Blockages or jams in the conveyor system can cause sudden stress on the belt, leading to breakage. Regular clearing of material jams is crucial.
- Stress Changes: The stress changes greatly when starting and stopping. The starting and stopping of the belt conveyor will also cause it to break. It is usually started under no load.
- ConveyorBelt Deviation: Material distribution is uneven, and the conveyor belt deviates. The belt conveyor has an unloaded section and an overloaded section, which causes uneven stress and causes belt breakage.
Belt Conveyor Management
Poor maintenance of the belt conveyor and lack of regular maintenance, including proper lubrication, cleaning, and inspection, can lead to wear and deterioration over time. Such as
- Some companies still need to establish corresponding technical files and work systems to manage belt conveyors, causing breakage accidents due to work negligence.
- More material transportation management mechanisms are needed. When the belt conveyor has steel drills, anchor rods, and other foreign objects involved in the belt during operation, it cannot be dealt with promptly and effectively, resulting in a belt breakage accident.
- Job responsibilities are not implemented strictly. In some enterprises, there is a situation in which job responsibilities are not fully implemented in management, causing the equipment to run in a sick condition, thus causing a disconnection accident.
Others
- Parts Damaged:The gear reducer is damaged, the hydraulic coupler sprays fluid or the motor reverses.
- Environmental Factors:Extreme temperatures, humidity, or exposure to chemicals can degrade the material of the conveyor belt, making it more prone to breakage.
- Age and Wear:Over time, the conveyor belt naturally wears out, and its structural integrity may decline, increasing the risk of breakage.
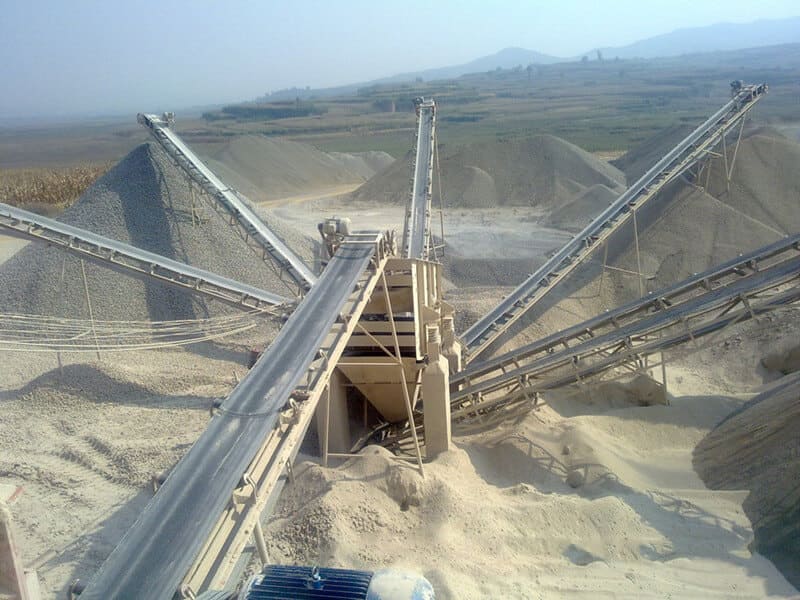
Belt Conveyor Breakage Prevention Measures
Preventing belt conveyor breakage involves a combination of proper maintenance, operational practices, and implementing preventive measures. Here are some measures to help prevent belt conveyor breakage:
1. Strictly control the quality of rubber materials
When selecting rubber materials, use products specified by the manufacturer and ensure that all purchased rubber materials have labels such as shelf life, certificate of conformity, manufacturing date, factory certificate, specifications, and models. If the rubber materials do not have labels, don’t use them.
In addition, when storing rubber, you should avoid direct exposure to strong light, store it in a cool place, and avoid contact with harmful chemicals. Corresponding identification work must be done before using the rubber material to ensure that its quality reaches the standard before it can be used.
2. Reasonably choose the length and type of joints
Most joint types are three-level full lap joints, and a few use two-level ones. Relevant experimental research shows that the retention rate of first-level and third-level full-lap joints is higher. The spacing between adjacent wire ropes will also differ if the same belt has different overlapping forms. The first-level distance is the smallest and gradually increases upward. The larger the spacing, the more conducive to improving the strength of the vulcanized joint. The choice of joint form should be determined based on a comprehensive comparison of many factors such as the belt type, belt strength, number of wire ropes, wire rope diameter, and spacing.
3. Strictly control the vulcanization process
Joint vulcanization is the last important process that determines the quality of the tape during installation. Accurately grasping its technical conditions is the key to ensuring joint strength and joint life. The vulcanization process’s technical conditions are mainly the vulcanization’s three elements: the vulcanization temperature. (Within the range of 142~148℃, it cannot exceed 150℃.), time and pressure. Suppose the vulcanization process’s technical conditions are not strictly or improperly controlled. In that case, it will cause quality defects such as insufficient sulfur, excessive sulfur, delamination, blistering, heavy leather, and belt deviation, adversely affecting future operation and maintenance.
4. Reasonable tailoring of rubber materials
Because rubber has a specific vulcanization shrinkage, its size can be slightly larger during the cutting process, but it should not be too small.
According to the tape model, the width of the surface tape and the core tape should be reasonably determined. The miter length should be included when determining its length if it is a miter joint. When cutting the rubber material, the distance between the backstops after fixing the joint is taken as the width of the surface glue. The width at both ends may differ, and the full length of the joint is its length.
5. Strengthen the management of belts
1) Establish a complete job responsibility system, shift handover system, patrol inspection system, joint acceptance inspection system, and equipment maintenance system.
2) Improve the belt conveyor’s file replacement, technical file management, on-site inspection, and maintenance records, and regularly analyze and summarize relevant data.
3) It must be ensured that staff have received systematic training and learning and can correctly master professional techniques to avoid improper subsequent operations.
4) Manage the transportation of materials well. Do not use belt conveyors to transport large pieces of gangue, metal, electromechanical equipment, and other items to prevent overweight, long, sharp, and hard objects from damaging the high-strength belts.
5) Do a good job maintaining the belt conveyor to ensure the idlers are flexible and complete to prevent the belt from wandering.
There are various reasons for belt conveyor breakage accidents in actual production. Correctly analyze the causes of the accidents and take adequate measures to deal with and prevent them to minimize the accident rate of belt conveyors.