Barite is a mineral composed of barium sulfate (BaSO4). It is usually colorless or milky white, but can also be found in red, yellow, blue, or gray shades. The most common use for barite is as a weighting agent in drilling fluids.
Barite use and beneficiation method depend on the ore type and end-use.
Barite Ore Types
It can divide barite deposits into four types. They are sedimentary, volcanic sedimentary, hydrothermal, and residual slope deposits.
Ore Types
Ore Type | Ore Characteristics | Main Minerals and Associated Minerals |
Sedimentary | Block or streak and pea-grained structures | Barite, quartz, clay minerals, pyrite, etc. |
Hydrothermal | dense, gray to white | Barite, pyrite, chalcopyrite, galena, sphalerite, hematite, fluorite, witherite, etc. |
Volcanic sedimentary | Barite, siderite, specularite, etc. | |
Residual slope type | Easy to choose, high grade | Barite, fluorite, calcite, quartz, etc. |
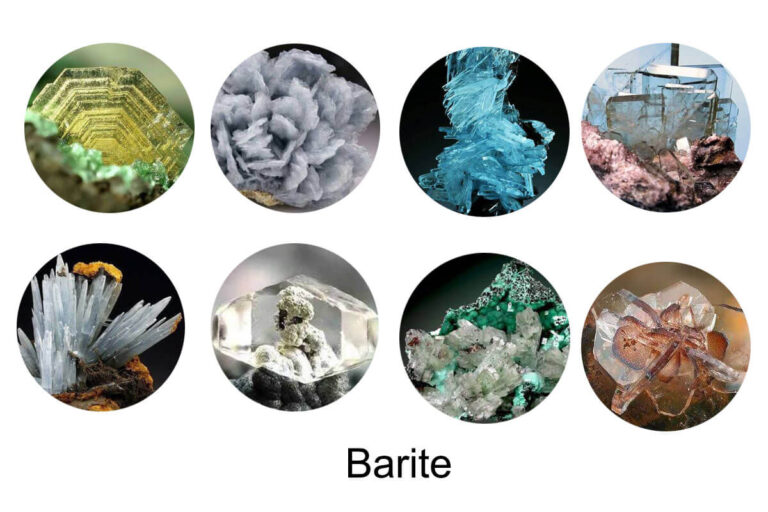
Process Characteristics & Uses of Barite
Barite is an important barium-containing mineral with large specific gravity (4.3-4.7) and low hardness (3-3.5). Its chemical properties are stable and insoluble in water and acid. Barite powder is mainly used in petroleum, chemical, paint, filler, and other industrial sectors. 80%-90% of them are used as mud-weighting agents in oil drilling. Following we list out its main uses.
The main use of barite
Application Field | Main Purpose | Remark |
Oil drilling | Circulation mud weighting agent in rotary drilling of oil and gas wells. | Cool the drill bit, take away the cut debris, lubricate the drill pipe, seal the hole wall, control the oil and gas pressure, and prevent the oil well from blowing out. |
Chemical | Production of barium carbonate, barium chloride, barium sulfate, barium white, barium hydroxide, barium oxide and other barium compounds. | These barium compounds are widely used in reagents, catalysts, sugar refining, textiles, fire protection, various fireworks, coagulants for synthetic rubber, plastics, pesticides, surface quenching of steel, phosphors, fluorescent lamps, welding flux, grease additives, etc. |
Glass | Deoxidizer, Clarifier, Flux | Increases optical stability, gloss and strength of glass. |
Rubber, plastic paint | Fillers, brighteners, weighting agents. | |
Architecture | Concrete aggregates, paving materials. | Heavy pressure buried pipes in swamp areas, instead of lead plates for shielding in nuclear facilities, atomic power plants, X-ray laboratories, etc., to extend the life of the road. |
Barite Beneficiation Method
According to the differences in ore properties, mine size, and use, there are mainly gravity separation and flotation methods. Gravity separation mainly includes washing, desliming, screening, jigging, shaking tables, spiral chutes, and other methods. The flotation is mainly positive flotation. Under the action of the flotation agent, the barite is separated from the impurities such as galena, sphalerite, pyrite, silica, and silicate.
The choice of barite beneficiation method is affected by the ore type, raw ore properties, mine size, use, etc., The main beneficiation methods currently used are shown in the following table. Generally, residual ore is easy to select, so the gravity separation method is preferred. The flotation method is also used for sedimentary ore and hydrothermal ore associated with sulfide ore, fluorite, etc., and gravity separation. Barite flotation commonly used anionic collectors: fatty acid salts, petroleum sulfonates or sulfates, etc.
The main beneficiation and processing methods of barite
Mineral processing method |
Mineral processing principle |
Application range |
Hand-selected |
Barite and associated minerals are different in color, density, etc. |
Select massive barite |
The density difference between barite and associated minerals |
Including washing, desliming, screening, jigging, shaking, and other processes that are mostly used for residual ores |
|
Flotation |
The difference in surface physical and chemical properties of barite and associated minerals |
Commonly used in sedimentary barite ores and hydrothermal barite ores associated with sulfide ores, fluorite, etc. |
Magnetic difference between barite and iron oxide minerals |
Mainly used to remove iron oxide minerals impurities |
Process Flow
It usually uses the gravity separation method to classify the residual barite ore. The process includes washing, crushing, screening, and through jigging or other gravity separation methods to get the barite concentrate. For sedimentary and hydrothermal barite ore, the gravity separation method still can not meet users’ requirements, and it is necessary to use flotation. Especially when barite is symbiotic with galena, sphalerite, pyrite, and other sulfide minerals, fluorite, calcite, etc., It can only be effectively separated by the flotation method.
General Requirements for The Barite Flotation Process
- Grinding fineness:Barite flotation generally requires grinding fineness-200 to be 85~90%. Usually, the first stage grinding classifier overflows into the cyclone and passes through the cyclone. The second grinding stage is carried out after classification, and the optimum grinding fineness needs to be determined by experiment.
- Stirring:Using a powerful secondary stirring tank is advisable.
- Flotation:The process is generally one rough sweep (some have no sweep) and five to six selection times. It can return the medium ore at one time or the first fine, and it will return the second fine in turn, concentrate and select the third to fifth fines again. Straight to the rear. It is a feature of barite flotation that the selection times of flotation are more.
Barite Flotation Reagent
The adjustment agents for barite flotation are mainly water glass and sodium carbonate. Sometimes when the ore is complex, other inhibitors are added. The collectors are primarily oleic acid, oxidized paraffin soap, sodium petroleum sulfonate, etc. The advantages of the agent in actual production are that the agent is conventional, the flotation cost is low, it is easy to operate, etc. Still, it has shortcomings: poor selectivity and difficulty achieving a higher concentration grade. The amount of foam in the concentrate is large, making it difficult to transport and concentrate, and it is easy to run out of the trough.
In conclusion, barite is an important mineral for many industries and has a wide range of applications. Its use and beneficiation methods vary depending on the application. However, regardless of the application, barite must be properly processed to ensure a high-quality product.