The ball mill steel ball is the medium for grinding materials in the ball mill equipment. The friction and friction between the steel balls of the ball mill and the material produce grinding and peeling effects. During the operation of the ball mill, whether the gradation of the steel balls in the grinding body is reasonable is related to the working efficiency of the equipment. Ensure that various balls have a certain proportion that can be adapted to the particle size composition of the material to be ground and that good grinding effects are achieved. Reasonable selection of the gradation of ball mill steel balls is an indispensable measure to improve the output and quality of ball mills. Let’s look at how to obtain a reasonable gradation of ball mill grinding body steel ball media and how to select ball mill steel balls.
Ball Mill Steel Ball Gradation Basic Principles
- Determine the steel ball gradation based on the particle size, hardness, grindability of the grinding materials, and the fineness requirements of the product. When the particle size of the materials to be ground is small, the grindability is good, and the product fineness is required to be fine, it is necessary to strengthen the grinding effect of the materials, and the diameter of the selected steel ball should be smaller. A larger impact force is required to handle ores with large hardness and coarse particle size, and more giant steel balls must be loaded. That is, the harder the material is, the larger the diameter of the steel ball will be.
- The surface shape of the mill lining is also one of the factors that need to be considered when matching balls. If the surface shape of the lining plate causes insufficient ball-carrying ability, the lifting height of the steel ball will be reduced, and the impact force will be reduced. At this time, the steel ball diameter should be selected to be larger—the larger the diameter of the mill, the greater the impact force. Choose a steel ball with a smaller diameter.
- If a double-compartment partition is used, the ball diameter should be smaller than that of a single-layer partition with the same discharge section.
- The diameter of the steel ball selected is related to the material throughput per unit volume in the mill. If the recycling amount is high, the diameter of the steel ball should be slightly larger; otherwise, it should be smaller.
- The mixed steel ball group composed of large steel balls of ball mill equipment has a larger void ratio than that of small steel balls. Generally, there are four levels of balls, with fewer big and small balls and a larger ball in the middle, “less at the two ends and more in the middle.”
We can also choose the appropriate ball mill steel ball configuration for the specific ore hardness. If the added material is a relatively hard ore, then when selecting the ball mill steel ball, we should choose a steel ball with a particle size of 5 times the ore; if The material is medium hardness ore, then the ball mill steel ball we choose is a model that is four times the particle size of this ore.
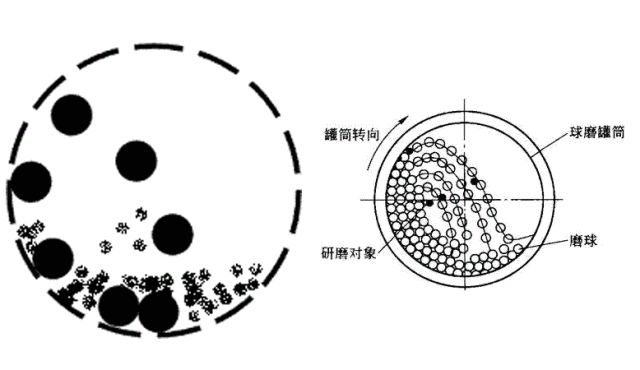
Factors to consider when mixing steel balls in ball mills
- Equipment model:Such as cylinder diameter and length;
- Production requirements: The user’s standard for grinding fineness of materials;
- Material properties: Refer to the initial particle size, hardness, and toughness of the material to be ground;
- Specifications: Pay attention to the specifications and do not blindly pursue large specifications.
Tips for adding steel balls to ball mills
The ratio of steel balls in the ball mill depends on the effective length of your mill, whether it has a roller press, the size of the feed particles, the lining and structure used, the expected sieve residue fineness and ratio, how many chromium balls to operate, and the rotation speed How much and other factors make a comprehensive judgment. After the ball mill is installed, the large and small gears of the ball mill need to be meshed, and the processing capacity must be gradually increased. After the ball mill has been running normally for two or three days, check the meshing situation of the large and small gears. When everything is normal, open the manhole cover of the ball mill and add the remaining 20% for the second time.
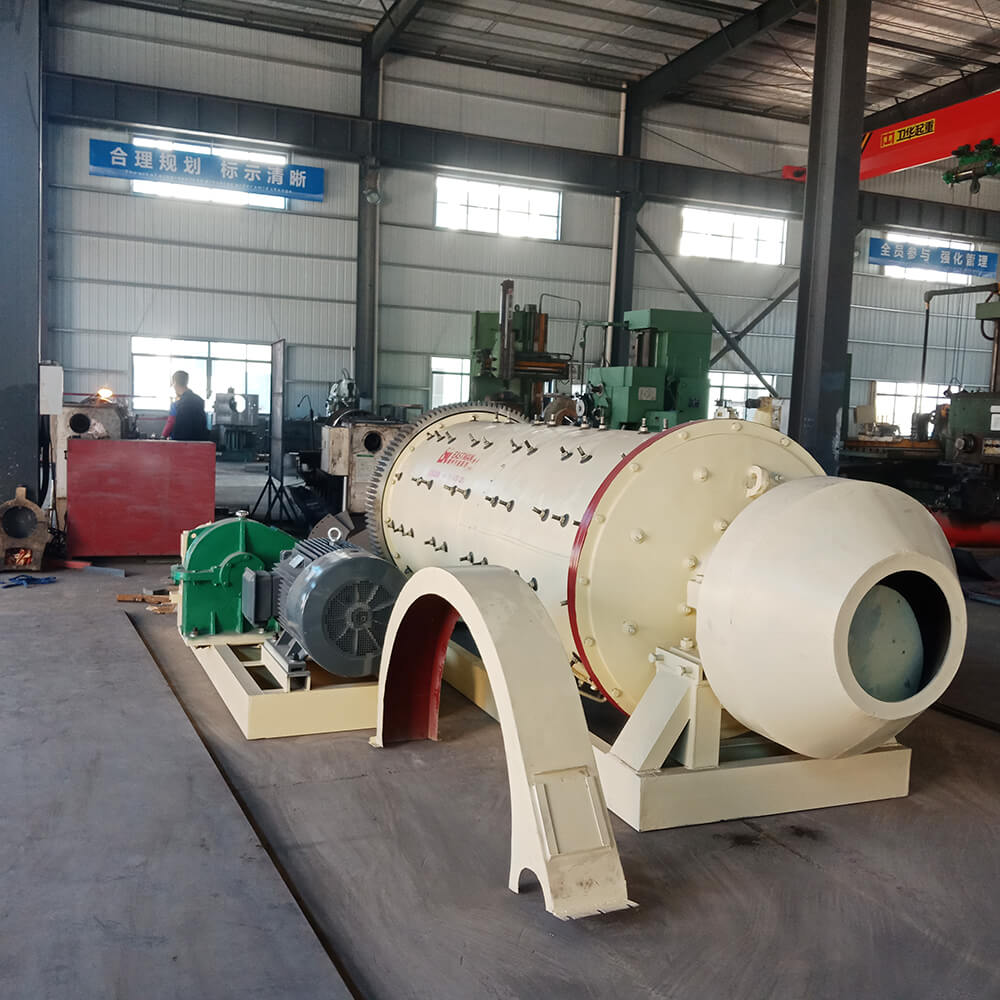
Ball Mill Steel Ball Grading Precautions
- During the normal operation of the ball mill, the reasonable friction generated between steel balls & steel balls, steel balls & ores, and steel balls & ball mill linings will increase the wear, causing large balls to be ground into small balls and medium balls to be ground into small balls. Therefore, under normal circumstances, there is no need to add small balls.
- The steel balls in the ball mill are constantly worn during operation. We must replenish the balls reasonably to maintain the ball charge filling rate and the reasonable ratio of balls and maintain the stable operation of the ball mill.
- The weight of the steel balls added is based on the quality of the steel balls. The quality of the steel balls determines the amount of ore added per ton. They are using new wear-resistant steel balls. Good quality steel balls are added based on the amount of ore processed per ton (that is, 0.8kg per ton of ore). Generally, steel balls are required to process one ton of ore (1kg-1.2kg).
In short, the ratio of steel balls in a ball mill is a relatively complex technical issue. Each mineral processing plant must carefully analyze its actual situation; through long-term research and accumulation, it can find the ball-filling ratio that suits it. In addition, the steel ball ratio also includes the ball diameter and quantity. The ratio is determined based on all the information. It must be just right. One point more is not enough, and one point less is not enough.
How To Choose Ball Mill Steel Balls?
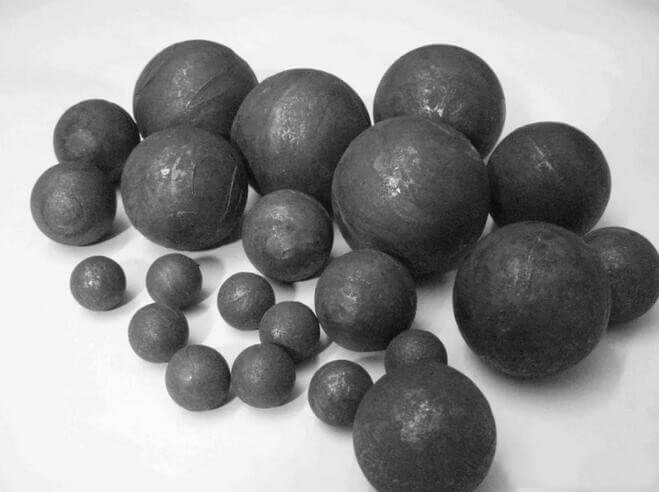
Choosing the right ball mill steel ball is crucial to the grinding efficiency and product quality of the ball mill. The ball mill steel ball is an important part of the grinding medium in the ball mill. It directly affects the grinding effect and the degree of refinement of the ore. When selecting ball mill steel balls, you need to consider the following factors:
1. The impact force of the steel ball.
First, let’s talk about the role of impact force. Steel balls are an essential medium mainly used to grind materials directly. Steel balls stop impacting and grinding during the operation of the ball mill and can grind materials into fine powder. When the steel ball’s impact force exceeds the material’s strength limit, the material will be crushed to achieve the purpose of grinding. However, excessive impact force will also consume a lot of energy on the lining plate of the ball mill. Therefore, when choosing a steel ball, its impact must be considered first.
2. The grinding force of the steel ball.
During the ball mill’s operation, the steel ball’s surface area is mainly relied on to make the material contact with the steel ball’s surface to improve the ball mill’s grinding efficiency. In particular, the fine grinding chamber that relies on the grinding action to stop grinding is critical. The size of the grinding force determines the thickness of the grinding fineness, so the grinding force of the steel ball is also vital.
3. The number of impacts of the steel ball.
The more collisions the ball mill steel ball has, the higher its grinding fineness and output will be. The number of impacts of the steel ball is critical, and the number of effects depends on the ball diameter of the ball mill. For materials that are difficult to grind, it requires a strong impact force, increases the number of impacts, and extends the grinding time of the material in the silo. In the actual purchase, we have to choose according to the grinding conditions of the ball mill.
4. Material storage capacity and squeezing force.
Through the gradation of large and small balls, the gaps between the steel balls are reduced, and the packing density of the steel balls is increased to have appropriate material storage capacity. On the one hand, it can control the flow rate of the material in the mill and extend the residence time so that it can be fully ground; on the other hand, it can extrude the material to facilitate the impact and crushing of the large ball.
Choosing suitable ball mill steel balls requires reasonable selection based on specific grinding conditions and ore properties. When we purchase a ball mill, we must choose suitable equipment based on our material conditions and finished product particle size requirements, and then add steel balls with good performance and cost-effectiveness according to the specific situation to ensure the grinding efficiency and performance of the ball mill. At the same time, regular inspection and maintenance of the ball mill and reasonable use and replacement of steel balls are also key measures to ensure the normal operation of the ball mill and extend its service life.