As we all know, no matter which mineral it is, its state of existence is not single but complex and diverse, so use various methods to select them. However, it is only possible for mineral processing equipment to extract some of the minerals you want, no matter which mineral processing method. Understanding the characteristics of each beneficiation equipment is of great significance to the beneficiation method. Now let’s talk about the main factors that affect the beneficiation effect of the 6s shaker.
First of all, the sorting principle of the mineral shaker is mainly based on the density difference between the minerals for sorting, so there are requirements for the particle size of the material and the specific gravity difference between the materials, and the particle size range is between 2mm-0.074mm. Better, if the particle size is below 0.074mm, the 6s shaker bed surface needs to be improved, and the 138 or 150 groove bed surface will be better for sorting.
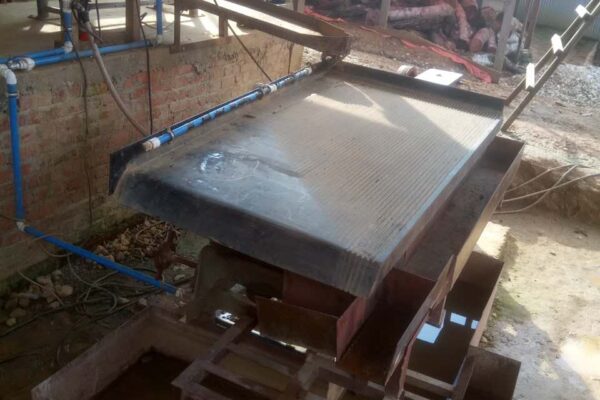
What are the factors that affect the selection effect of 6s shaker?
1. The Degree of Dissociation of Minerals
Insufficient mineral dissociation is one of the main reasons that directly affect the sorting effect of beneficiation equipment, and the 6s shaker is no exception. Of course, each mineral’s degree of dissociation is different, requiring professional analysis before beneficiation.
2. Stroke and Stroke Times
The stroke and the number of strokes mainly affect the loosening, stratification, and selective transportation of ore particles on the bed. The stroke and the number of strokes are two critical factors for each other. When selecting fine-grained materials, it is advisable to use small and high strokes; the opposite is true when choosing coarse-grained materials. For coarse-grained materials (2.0~0.074mm), the stroke can be adjusted between 15-27mm, and it adjusts the stroke rate between 250^280 times/min. For slime, the stroke is 11-13 mm, and the stroke rate is 350-360 strokes/min. However, the most suitable stroke times are generally determined through experiments and are usually not adjusted during operation.
3. Feeding Method and Pulp Concentration
The wrong ore feeding method and concentration have a direct relationship with the sorting effect of the 6s shaker. The ore feeding method of the 6s shaker generally includes:
- Belt conveying of materials.
- Screw conveyor feeding.
- Slurry pump feeding through shunting barrels or ore boxes.
The feeding concentration of coarse-grained minerals can be around 30% while controlling the feeding concentration of fine-grained minerals below 20%. The specific effect should be observed and adjusted in daily production. The typical feeding concentration of the shaker is generally 15%~30%.
The ore feeding volume is also an essential factor in the operation of the shaking table. If the ore feeding volume is constant, the ore feeding concentration is too low, and the pulp volume increases, which will cause the beneficiation recovery rate to decrease. If the amount of ore to be fed is certain, and the concentration of ore to be provided is too large, the recovery rate of beneficiation will also decrease. The amount of ore to be fed also depends on the particle size of the ore to be processed.
4. The Water Supply of The 6S Shaker
The water supply mentioned here refers to the water supply to the tank at the end of the shaker. The coarse-grained mineral water supply can reach 3-5 cubic meters in one hour while controlling the fine-grained water supply within one cubic meter. Too much water and too little water significantly impact mineral sorting.
5. The Lateral Slope of The Bed Surface of The 6S Shaker
Increasing the slope can increase the speed of the water flow. Generally, when dealing with fine-grained materials, the slope should be smaller, and when dealing with coarse-grained materials, the slope should be larger. It can adjust the slope in the range of 0°~10°. For the slope of different materials, reference the following values: 3.5°~4° for coarse-grained grades less than 2 mm; 2.5°~3.5° for materials less than 0.5 mm; less than 0.1 For fine-grained materials of millimeters, use 2°~2.5°; for slime (0.074 mm), use about 20 degrees. It should note that the choice of slope should work well with the amount of water. The water flow in the area is evenly distributed, without waves, and the ore sand is not piled up.
6. Feeding Properties
The density, particle size, and shape of the ore particles in the shaking table feed greatly influence the sorting index. When the density difference between heavy and light minerals is greater than 1.5, it can successfully sort on a shaking table. It is easily washed spherical-like ore particles and coarse particles away by water. We generally use shaker tables to classify materials, namely hydraulic classification. In the products obtained by hydraulic classification, the average particle size of heavy minerals is much smaller than that of light minerals, which is conducive to separation and stratification and improves the separation effect.
7. Receiving Minerals
Access to mines is also a significant problem that plagues many mine owners. If you master the ore dressing principle of the 6s shaker, pay attention to the distribution of mineral belts on the shaker bed surface during production. Use the standard 6s shaker receiving device to solve this problem quickly.
The above factors affect the beneficiation effect of the 6s shaker for your reference and study. Every kind of beneficiation equipment looks simple, but it has a lot of knowledge when used. As miners, we must maintain an open-minded and studious attitude toward mineral processing knowledge, technology, and the use of equipment, and we will continue to improve. As a professional mineral processing equipment manufacturer, we look forward to exchanging and learning with mining people worldwide.