The flat plate high gradient magnetic separator is a new type of equipment manufactured by JXSC Mineral. The design and development of the whole machine integrate physics, fluid dynamics, and magnetic structure mechanics. It has extremely high magnetic induction strength, and the maximum magnetic field reaches 15000GS. The invention of this equipment can fully meet the standard requirements for iron removal in the following fields, and the construction cost is only one-tenth of that of the vertical ring high gradient magnetic separator. The high-cost performance is something that the vertical ring magnetic separator can never surpass. It fundamentally solves the global bottleneck problem that traditional magnetic separators are prone to blockage and severe cutting when dealing with small particles. It is a disruptive improvement in the high-gradient magnetic separator industry. Please follow us to get to know the plate high gradient magnetic separator.
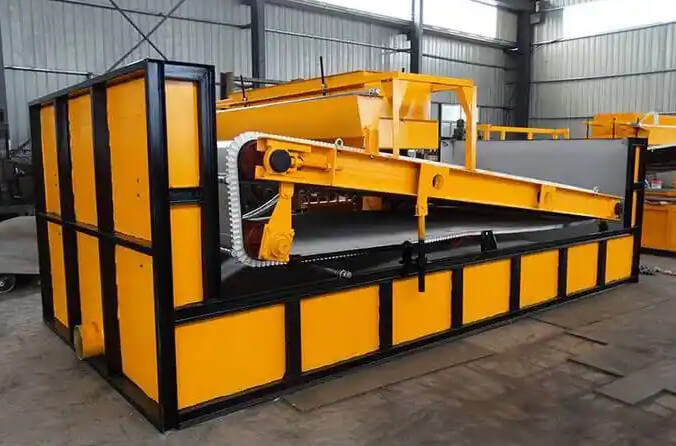
What Fields and Materials Are it Applicable To?
Application fields and applicable materials of plate high gradient magnetic separator are as follows:
Application
The flat plate high gradient magnetic separator is widely used in the following scenarios:
- Metal ore sorting: wet sorting of weakly magnetic minerals such as hematite, limonite, manganese ore, ilmenite, etc.
- Non-metallic ore purification: iron removal and purification of non-metallic minerals such as quartz, feldspar, kaolin, fluorite, etc., which can reduce the Fe₂O₃ content from 0.73% to 0.5%.
- Environmental protection and industry: wastewater treatment (such as steel plant wastewater), chemical raw material cleaning, and coal impurity removal.
Flat plate high gradient magnetic separators can be used for iron removal of materials such as coal, mining enterprises, decorative building materials, etc.
Applicable Materials
The flat plate high gradient magnetic separator is mainly suitable for the ore selection of weakly magnetic minerals with a particle size distribution of less than 5 mm and the removal of iron from mining materials, such as quartz powder, quartz sand, potassium feldspar, nepheline, fluorite, sillimanite, spodumene, porcelain clay, manganese ore, weak hematite, pyrrhotite, roasted ore, ilmenite, hematite, limonite, siderite, ilmenite, chromite, wolframite, tantalum-niobium ore, tailings, etc.
What Parts Does A Plate High Gradient Magnetic Separator Consist Of?
Structure
The flat plate high gradient magnetic separator is mainly composed of a support frame, flat plate magnetic separation equipment system, feed mixing system, water system, iron unloading system, adjustment system, and other structures. During operation, the material inflow and iron unloading system are in reverse flow, and the non-magnetic material automatically flows to the feed port according to the principle of physical structure and is completely unloaded after unloading and cleaning. The magnetic material is attracted by the strong electromagnetic field over a long distance, a long area, and multiple times, and flows back to the iron outlet through the iron unloading system, and is completely unloaded after unloading and cleaning.
What Are The Performance Characteristics of The Plate High Gradient Magnetic Separator?
Performance Characteristics
1. The magnetic system of the plate high gradient magnetic separator adopts advanced computer simulation design and adopts the repulsive magnetic pole arrangement structure to effectively ensure the maximum adsorption area and adsorption capacity of iron within the working range.
2. The permanent magnetic material is made of high-strength rare earth plastic anti-static forceps to form a super-strong transformer frame. The plastic anti-static forceps have high purity, large usage, strong magnetism, and the maximum magnetic induction intensity reaches 15000gs. It is a disruptive innovation in the high-gradient magnetic separator industry, and its performance is world-leading. The entire mechanical optimal control design, the magnetic system adopts a sealed structure, anti-oxidation, to ensure that the magnetic loss of the strong magnet transformer frame in extreme environments does not exceed 5% within ten years, and does not affect normal use.
3. The drive part adopts a high-performance step-less electromagnetic speed regulation motor, which is fully automatic and continuous to work and unload iron, saving manpower and reliable operation. The entire mechanical feeding system adopts an electric motor mixing structure, so that the material is evenly distributed when entering the magnetic separation area and the coal slurry concentration meets the requirements of the ore dressing plant, making the screening effect more effective.
4. The entire mechanical water supply system adopts a single overall water inlet position, and the valve controls each water supply point. It is convenient for customers to provide water supply equipment, and each valve can be opened and adjusted according to specific needs.
5. All the material passing or touching positions are made of stainless steel or non-magnetic materials to effectively prevent the secondary contamination of the material by the equipment. When necessary, the key positions can be treated with wear resistance.
6. This equipment can make the falling ore evenly distributed on the magnetic separation mechanism, and will not accumulate into blocks. During the magnetic separation process, the ore can be turned with the change of the magnetic pole, which greatly improves the accuracy of ore purification.
7. The entire mechanical structure can be made into two structures: open or fully enclosed according to the on-site conditions. It can adapt to different customer and on-site standard requirements.
What Factors Should Be Considered When Choosing A Plate High Gradient Magnetic Separator?
The plate high gradient magnetic separator has become the core equipment for weak magnetic mineral processing due to its high magnetic field strength, flexible adjustment ability, and efficient sorting effect. Users need to pay attention to the following factors when choosing:
- Mineral characteristics: select the appropriate model according to the mineral particle size and magnetic strength;
- Customized requirements: customized configuration of functions such as magnetic field strength, belt speed, slope adjustment, etc.;
- Maintenance cost: give priority to wear-resistant belts and automatic cleaning system models to reduce long-term operation and maintenance costs.
The high-gradient plate magnetic separator has brought revolutionary changes to the field of mineral purification with its excellent performance and efficient separation ability. Its appearance has not only improved the utilization rate of mineral resources but also promoted technological progress and industrial upgrading in the mining field. In the future, the flat plate high-gradient magnetic separator will develop in the direction of intelligence, efficiency, and environmental protection. Technological innovation and application expansion will promote its widespread application in traditional and emerging fields. By optimizing the magnetic system design, improving equipment performance, and expanding application scenarios, the magnetic separator will play a greater role in mineral processing, resource recovery, environmental protection, and other fields.